SMS group, synonymous with the term ‘Innovation’ in the World of Metals, has a rich history of ‘150 Years of Shaping the Future’. From a small forging company and supplier to a local industry, it has developed into a global technology company that has had a significant impact on the development of the metal industry, making itself a truly international company. The group is continuously working on developing environmentally friendly solutions to reduce carbon emissions in the production and processing of metals. Recently, they announced the establishment of a new workshop in Gujarat, India. This was revealed by Mr. Bernhard Steenken, Chief Sales Officer, APAC & MEA Region, SMS group, during an interaction with Tube & Pipe India magazine at the international trade fair for Tube & Pipe in Düsseldorf, Germany, this year.
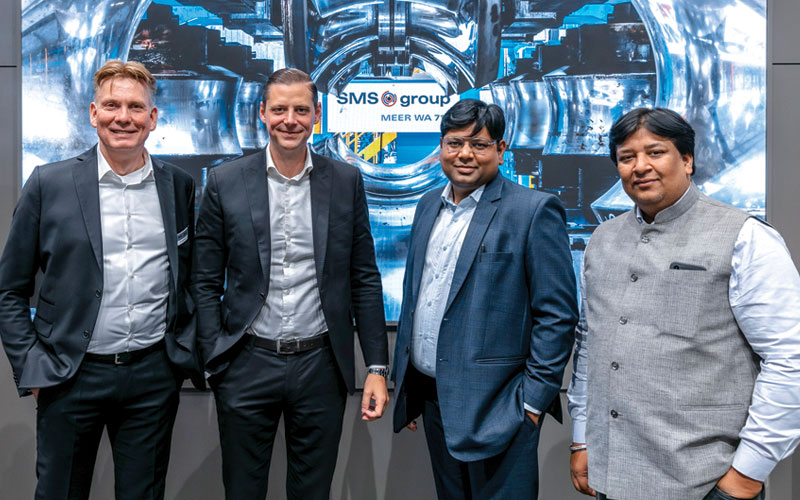
Tube & Pipe India: Discuss SMS group’s strategy for growing its presence in the global tube and pipe industry.
Bernhard Steenken: SMS group has opened branches and subsidiaries in the main markets. We are present in 31 countries, representing more than 80 percent of global steel production. There are two key drivers for our business. Decarbonization is one of the most important drivers of our strategy where we see huge growth potential and has been affecting all industries. Governments across the globe are looking for green solutions to reduce carbon emissions and we believe that the green transformation of the steel industry is a marathon, not a sprint.
Our lighthouse projects like H2 Green Steel and thyssenkrupp Steel will prove that climate-neutral steel production is possible. The H2 Green Steel Facility in Sweden will be the first worldwide green steel plant starting from iron ore with a fully electrified process chain thanks also to the adoption of green hydrogen in the primary stage. The new green steel plant will be fully equipped with plant technology from SMS group. This hydrogen-based direct reduction plant will be fully integrated, transforming virgin raw materials into finished steel. This significant step will push the metal industry to the next level in terms of decarbonization.
Additionally, we have supplied a new CSP® Nexus plant to JSW. For the first time, hot strips and plates for shipbuilding, wind towers, heavy pipeline grades (API), or alike with a maximum width of 2,600 millimeters can be produced on a single plant that comprises casting and direct rolling. The hot strip thickness range of 2.0 to 32.0 millimeters is exceptional and offers JSW Steel (Dolvi Works) a unique opportunity to open up new markets at a competitive cost level, particularly in the field of “green plate” production. With parameters like these, the CSP® Nexus plant for JSW Steel (Dolvi Works) is not only setting standards for thin slab casting and rolling plants but also for conventional hot strip mills.
The demand for tubes has been rising exponentially, and we expect the market to pick up again. In India, there is significant growth in infrastructure. For instance, the CSP® Nexus plant for JSW Steel (Dolvi Works) supplies high-quality pre-material to ERW (Electric Resistance Welding) tube welding lines. These lines then utilize this pre-material to produce structural and piling tubes. These end-products are crucial for infrastructure construction, providing essential components for pipelines, structural supports, and other critical infrastructure elements, thereby supporting robust and reliable infrastructure development. Therefore, the market outlook for pipes is quite positive.
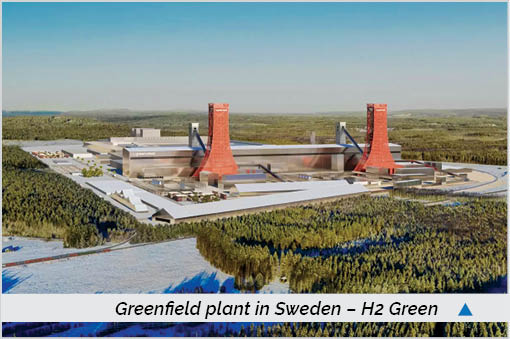
Customer needs have changed in recent years, and the SMS group has been adapting to these changes. Customers are increasingly requesting a transition to renewable energy supplies, incorporating more renewable sources into the energy mix, and facilitating the transport of hydrogen and CO2. In response, SMS group engineers and provides innovative solutions to enable the transport of renewable energy sources. Their green solution portfolio, such as Viridis, helps in the overall reduction of carbon footprints.
Transporting hydrogen or CO2 presents several challenges. Hydrogen, being a smaller molecule, has a higher risk of leakage and a wider flammability range compared to natural gas. It requires approximately three times the volume to deliver the same energy, necessitating larger volumes or higher pressures during transportation. Additionally, hydrogen’s reactivity can lead to material embrittlement. Overcoming these challenges requires a very controlled and stable transportation process, with the right choice of materials and pipe dimensions, especially wall thickness. SMS group provides tailored solutions for the transportation of hydrogen in the tube and pipe industry. By selecting appropriate technologies for each plant, SMS enables the manufacturing of pipes based on specific requirements. Some tube and pipe customers are already successfully operating in the hydrogen market using SMS solutions. For example, the JCO press, combined with the shape system and the subsequent expander, allows for the production of high-quality pipes with tight tolerances, even in difficult diameter-wall thickness ratios.
The second key driver is our service business which includes automation, digitalization, spares, repairs, and technical outsourcing. By 2030, we plan to increase our business share to 50 percent from the equipment business and 50 percent from the service business.
Decarbonization is our joint duty, not just in our industry but in every industry. We are always working to enhance our equipment with the latest technology to reduce the carbon footprint.
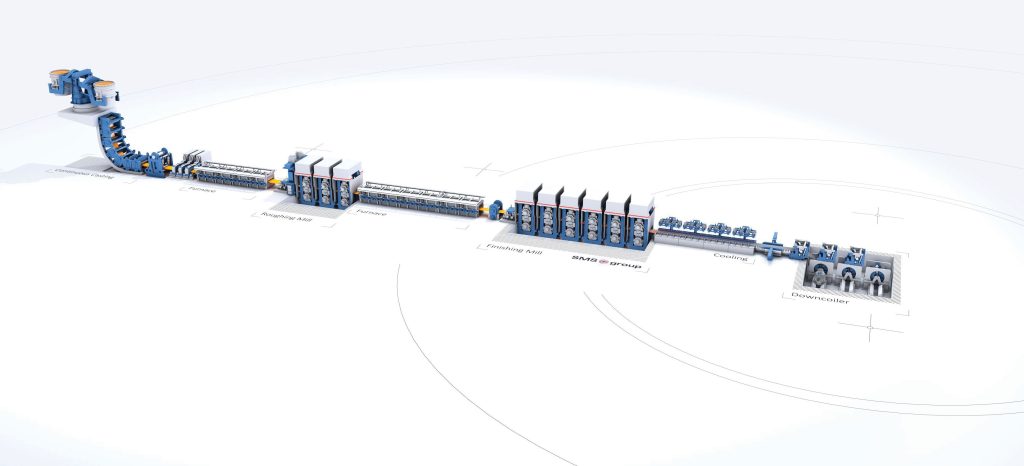
TPI: How do you help your customers achieve better efficiency on various fronts?
BS: Our “life cycle improvement” department goes beyond equipment supply. We support customers throughout its life, leveraging expertise from operations and engineering. We’ve developed new models like outsourcing maintenance (offline or online with cost-per-ton contracts) which is gaining traction in India. Additionally, our automation and digitalization team helps improve plant operations through transparency tools and best practices, enhancing customer decision-making. Technology and innovation are fundamental cornerstones of the SMS group. Our new solutions ensure sustainable, competitive advantages and therefore, future revenue and growth.
We integrate our three Centers of Excellence – electrics/automation, sms digital, and technical services – into one comprehensive entity automation, digital & service solutions (SX), to streamline organizational structures and foster collaboration. Our goal is to provide advanced integrated solutions that strengthen customer ties and our profitability, by providing tangible benefits in both tailor-made business and direct service.
Our lighthouse projects like H2 Green Steel and thyssenkrupp Steel, JSW Steel will prove that climate-neutral steel production is possible.
TPI: Please elaborate the group’s approach towards the ESG framework.
BS: Decarbonization is our joint duty, not just in our industry but in every industry. We are always working to enhance our equipment with the latest technology to reduce our carbon footprint, not only by integrating DRI steelmaking processes that utilize natural gas or hydrogen but also by electrifying our entire suite of equipment. By harnessing green electricity, we are making a substantial contribution to the decarbonization of steel production, demonstrating our commitment to sustainable industrial practices.
With the potential emergence of green steel plants in India, SMS group stands ready to assist the Indian steel industry in its decarbonization efforts. Leading steel manufacturers such as Tata Steel, SAIL, and JSW Steel have already initiated the first steps towards this transformation. The economic incentive for complete decarbonization isn’t strong yet. For instance, a large Indian steel exporter with five million tons of exports wouldn’t need to decarbonize its entire production; only the five million tons for export. Additionally, the growing Indian automotive industry might create a business case for green steel in the next five to ten years, but not in the bulk commodity market. SMS group’s expertise and technologies are pivotal in enabling this targeted approach to sustainable steel production.
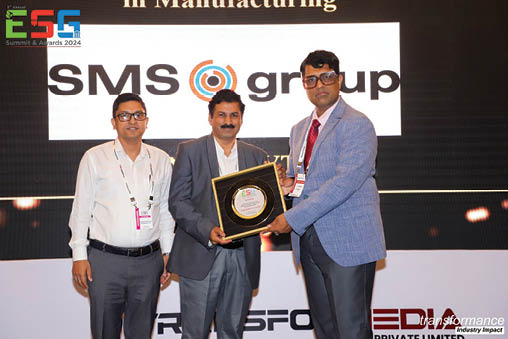
Currently, blast furnaces are the dominant technology for producing virgin steel in India. Scrap availability is limited, making blast furnaces the technology of choice. However, even for blast furnaces, technologies are being developed to reduce their carbon footprint. For instance, we have recently signed an MoU with TATA Steel who chose Paul Wurth’s EASyMelt as a key CO2 emission-reduction technology to be implemented at Tata Steel’s blast furnace E in Jamshedpur, India. In the first step, we will install a second ring to inject syngas into the furnace leading to approximately 30 percent CO2 reduction. In the second phase, we will replace the hot stoves with plasma torches to increase the temperature to 2400 degrees celsius as we need energy in the process coming from electrical energy via plasma torches which can reduce 60 to 70 percent of CO2 emissions. With this process, carbon capture will become economically feasible. Earlier, the CAPEX was too high for carbon capture using these technologies.
On the operational side, we try to bring our operations to maximum efficiency. Maximum efficiency cannot be achieved without huge investments. With maximum efficiency, CO2 emissions will be reduced while increasing the profit margins. At SMS group, we have made it our mission to create a carbon-neutral and sustainable metals industry. We supply the technology to produce and recycle all major metals. This gives us a key role in the transformation towards a green metals industry.
Recently, SMS group was honored with ESG Awards the 5th ESG Summit & Awards by Transformance held at Holiday Inn International Airport, New Delhi. The event was a gathering of industry leaders, sustainability experts, and corporate visionaries who are shaping the future of environmental, social, and governance (ESG) standards. Under 3 distinguished categories, the group was recognized for its commitment to sustainability and social responsibility: ‘Best ESG Initiative to Improve Communities/Cities’, ‘Best ESG Initiative to Reduce Carbon Footprint’ and ‘Best ESG Initiative to Improve Employment Quality.’
We’re excited to announce our new workshop in Gujarat. Supported by the Gujarat and national governments, the initiative aligns with ‘Make in India’ and ‘Vibrant Gujarat’, signaling strong governmental backing for industrial advancement.
TPI: How does SMS group manage to meet the diverse needs of different markets?
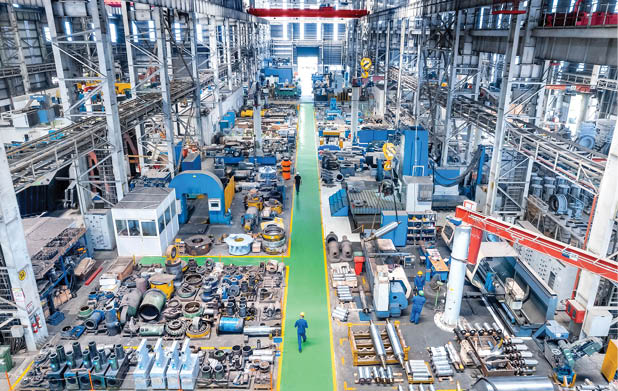
BS: Catering to a diverse market is both our strength and weakness. However, it presents a unique challenge. We offer a wide range of technologies, including upstream, downstream, flat products, and long products. Two or three years ago, we implemented a new structure to address this increasing complexity. Previously, we were organized as business units, where each unit was responsible for the entire product lifecycle, from product development to market execution. However, due to the growing complexity and geographical distances, this structure became inefficient. For example, a product team based in Germany or Italy might be too far removed from the needs of customers in other regions, especially considering time zone differences. To address this, we have adopted a regional structure with customer-facing teams. As part of the regional team, my role is to gather customer feedback. We are also responsible for the profit and loss (P&L) of our region, which is directly tied to our customers and projects. We manage the integration of technologies, which are primarily driven by our technological experts who are then deployed to the region. We have a highly skilled workforce, particularly in India, where we have around 2,000 employees supporting our broader APEC and MEA region (Asia Pacific, Greater India, Middle East, and Africa).
Also Read: Shalimar Paints: Lending Hues to Tube & Pipe Industry
TPI: What kind of further developments can we expect from the group in the coming years?
BS: We’re excited to announce our new workshop in Gujarat, India! This significant investment strengthens our presence in the rapidly growing Indian market. With operations starting in 2025, this workshop complements our existing state-of-the-art facility in Bhubaneswar and Khorda. The strategic location on the western coast of India improves logistics and caters to the booming economic development in the region. We’re actively hiring automation and mechanical engineers to support our expansion in India, recognizing it as a key market for the present and future.
This new workshop will be dedicated to producing key equipment for the international market, with a focus on production lines for flat and long steel products and forging plants. The facility will also provide localized repair and service solutions, serving major clients like AM/NS India and JSW, with potential future investments from POSCO and Adani promising to transform the region’s industry.
The workshop is set to initially employ 500 people, with the potential to expand to over 2,000 direct and indirect jobs. Collaboration with educational bodies will ensure a skilled workforce, with a horizontal deployment strategy ensuring practical training in manufacturing protocols.
Starting with an investment of 25 million euros, the project may increase to 40 million euros in line with production expansion. Supported by the Gujarat and national governments, the initiative aligns with ‘Make in India’ and ‘Vibrant Gujarat’, signaling strong governmental backing for industrial advancement.
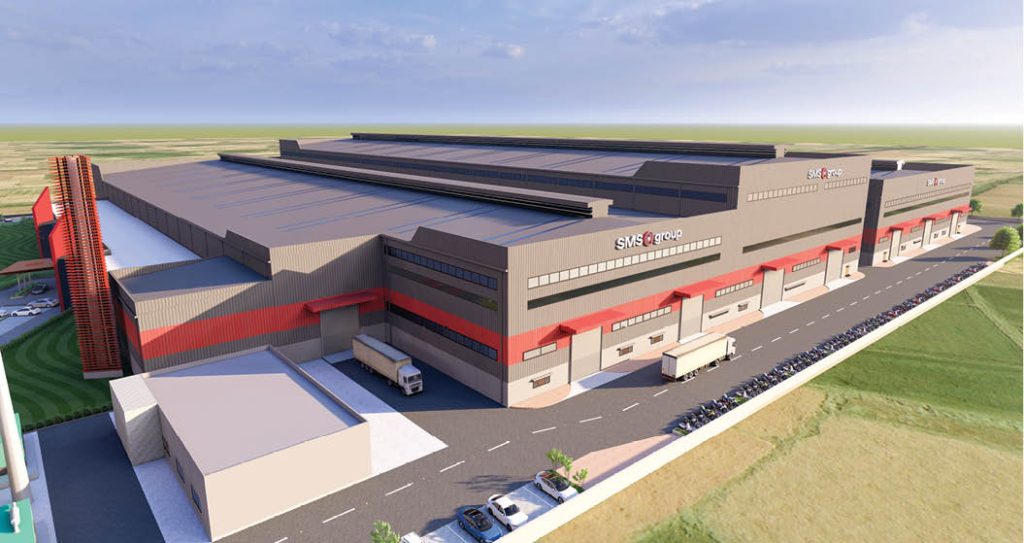