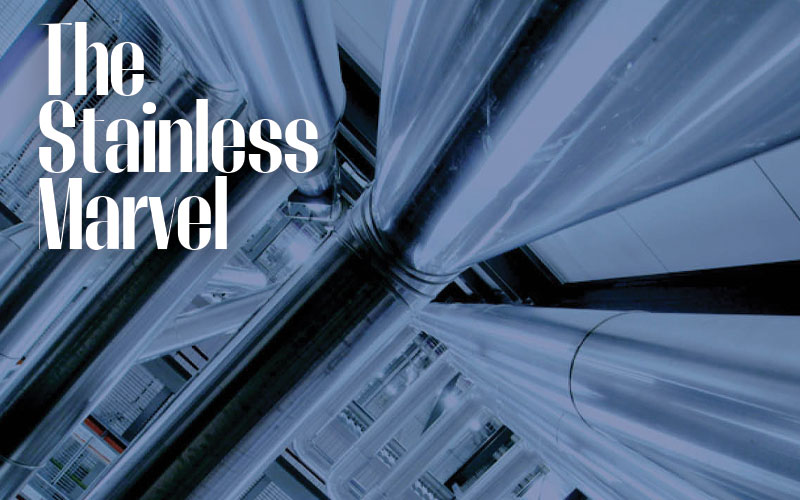
Over a century since its discovery, stainless steel has become a vital component of contemporary life, attributed to its resistance to corrosion, mechanical strength, versatility in shaping, aesthetic appeal, hygienic properties, and recyclability. These attributes render it appropriate for a wide range of applications. The establishment of hot and cold rolling facilities in the 1950s significantly boosted its production. However, in India, its use was largely confined to kitchenware, and the nation’s demand was primarily satisfied through imports until 1978.
Between 1980 and 2020, the demand for carbon steel increased at a consistent rate of 2.42 percent, whereas the demand for stainless steel experienced a significant rise of 5.13 percent, indicating a notable change in material preferences. Currently, stainless steel is utilized across various sectors, including tubing and piping, automotive manufacturing, and construction. Its unique properties have led to a substantial increase in the demand for stainless steel pipes and tubes, particularly in applications that involve corrosive substances, elevated temperatures, and high contaminant levels. The benefits of stainless steel include its ease of cleaning and minimal maintenance requirements over time.
The global market for stainless steel pipes and tubes, categorized into seamless and welded types, was valued at approximately USD 34.25 billion in 2022 and is projected to reach around USD 48.81 billion by 2030, as reported by Zion Market Research. In 2023, the oil and gas sector commanded the largest market share, contributing significantly to global revenue. The anticipated increase in investments for cross-country oil and gas transportation pipelines is expected to drive demand for these products throughout the forecast period. Additionally, the chemicals and petrochemicals sector is expected to experience substantial revenue growth. The construction industry also plays a crucial role as an end-user, utilizing stainless steel for various applications such as building structures, foundations, balconies, and railings. The trends of rapid urbanization and industrialization, particularly in developing nations, are likely to further enhance growth in this segment during the forecast period.
It is generally understood that the market’s growth potential may be constrained due to the substantial costs associated with initial production investments. The necessity for specialized raw materials, coupled with the inherent complexity of the alloy, are identified as primary factors that may discourage new entrants into the industry. As the sector becomes more structured or as regulatory measures are implemented, these barriers could increase. The forthcoming India Carbon Market (ICM) will require all obligated entities, including those in the iron and steel sector, to engage in mandatory emissions monitoring. This monitoring and reporting will encompass various aspects, including the identification of emission sources, the formulation and execution of monitoring plans, data collection on activities, application of emission factors, fuel quality assessments to ascertain emissions factors, and the calculation of both absolute and intensity emissions, along with verification procedures and requirements. Given that the steel industry contributes 10-12% of India’s total emissions, the government considers the decarbonization of this sector essential for the country to achieve its climate objectives.
The structure of the steel industry in India markedly differs from that of other nations. In developed countries, there is a greater reliance on scrap materials in total steel production, a high utilization of pellets, a less carbon-intensive energy grid, and the availability of low-carbon fuels such as natural gas at reasonable prices. In contrast, India faces challenges with limited scrap availability and high costs associated with natural gas. Furthermore, Indian integrated steel plants (ISPs) depend on captive coal-based thermal power plants, which exhibit a significantly higher emissions intensity compared to the cleaner energy grids found in developed nations. The Indian steel sector is compelled to utilize coal-based blast furnaces and rotary kilns for steel production due to the absence of affordable alternatives. It is anticipated that the investment required for the future production of green stainless steel tubes and pipes will be considerably larger.
Numerous challenges persist in the market, with several critical issues remaining unresolved. The ongoing crisis affecting shipping routes in the Red Sea has adversely impacted nations. This situation has led to increased cargo travel distances and elevated freight rates, consequently driving up costs. Several major Indian producers have scaled back their exports to key markets in response to surging shipping expenses and extended shipping durations of three weeks. Maersk has redirected its vessels away from the Suez Canal, which typically accommodates 15% of global shipping traffic under normal conditions. In India, the industry confronts various obstacles that could impede growth and diminish market competitiveness. A significant challenge arises from competition with lower-priced imports, prompting the government to recently implement anti-dumping duties. Additionally, the sector continues to struggle with the volatile prices of raw materials, such as nickel and chromium, while also striving to maintain consistent product quality amid variations in raw material standards.
Also Read: Sambhv Steel Tubes to Expand Product Portfolio with New Facility in Chhattisgarh
Since 2014, the Indian steel industry has operated as a deregulated sector, without any government subsidies. However, to foster the sector’s development and support the ‘Make in India’ initiative, the government has implemented several policy measures. One key initiative is the Production Linked Incentive Scheme for specialty steel. This scheme aims to promote domestic manufacturing of specialty steel and reduce imports by attracting capital investments. The anticipated outcomes include an additional investment of Rs 29,500 crores and the creation of around 25 million tonnes of specialty steel production capacity.
The Make in India initiative and the PM Gati-shakti National Master Plan are designed to increase participation from various sectors like railways, defense, petroleum, housing, civil aviation, and agriculture to boost steel use, demand, and investment. These steps are part of a broader effort. Amid ongoing challenges and the pressing need for the industry to be more sustainable, many companies have adopted new innovations and made significant investments, showing their commitment for the long term. This suggests that the stainless steel industry will stay strong and be able to handle difficult times.