BLM GROUP is one of the leading manufacturers of high precision and high performance tube laser cutting and sawing machines, CNC bending and end-forming machines in the world. The company serves various industries such as automotive, aerospace, agriculture and home appliances among others. In a conversation with Tube & Pipe India, Mr. Maurizio Toselli, Sales Director BLM GROUP shares interesting insights about the company’s technology and Industry 4.0 solutions.
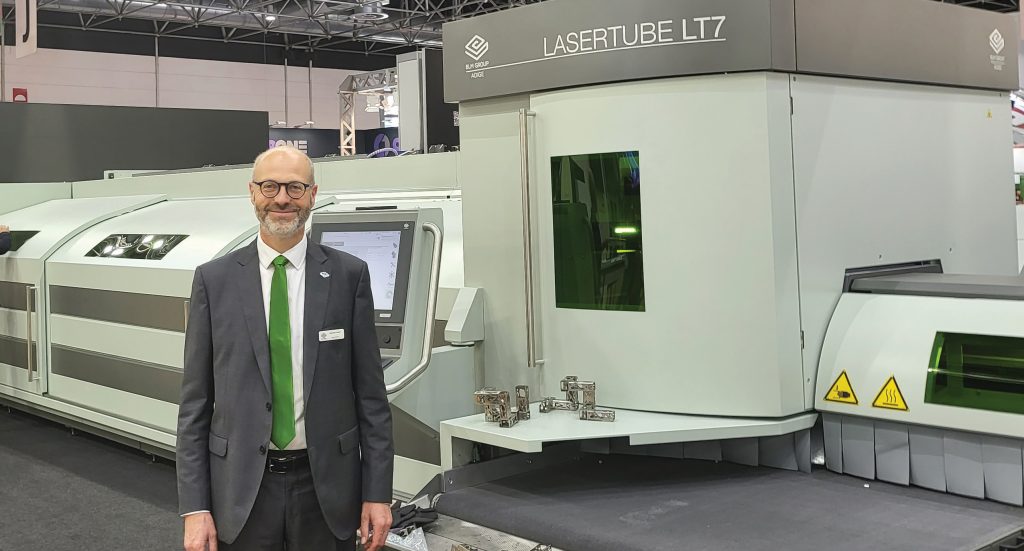
Tube & Pipe India: Please present a brief overview of BLM Group, its specializations, and some notable accomplishments.
Maurizio Toselli: For more than 60 years, BLM GROUP has been contributing to the growing challenges in tube processing with its knowledge from bending to shaping, to laser cutting before and after the forming process, and disc cutting.
Over the years, BLM GROUP has increased its know-how with greater machine-software integration to meet our customers’ needs with a wide range of products that fit into the production process of Industry 4.0. Our products have won the trust of customers, which is why today BLM GROUP has more than 800 employees worldwide.
Many customers come back to us after buying one of our products, to purchase another product line, or to strengthen their machine fleet. This, for us, represents a source of great pride.
TPI: Please describe the product portfolio and key capabilities of the company – with regard to manufacturing and technological innovations, especially for the tube industry.
MT: BLM GROUP can offer its clients a machine fleet distinguished by technology:
Lasertube: We have 2D and 3D laser cutting systems for tubes, bars and profiles with diameters ranging from 12mm to 610mm and maximum lengths of 18m. It is a versatile solution that combines multiple machining operations in a single environment. This allows the customer to speed up the assembly through easier interlocking and fastening, reducing total processing costs.
3D Cutting Cells: We provide a 5-axis laser or robot laser cutting system for processing three-dimensional parts. Cutting cells can be equipped with robot manipulators to process curved or hydroformed tubes without manual repositioning – all to the benefit of precision and productivity.
Sheet laser cutting: These machines allow cutting sheet metal of any material (mild steel, stainless steel, aluminum, copper, brass) with different thicknesses. Sheet metal laser systems are designed for high performance, low maintenance and low energy costs, thanks to the fiber laser source of up to 12 kW and the sensorized cutting head.
Tube bending: It includes a wide range of bending machines: right and left bending in process, right bending or left bending machines capable of processing tubes up to 150 mm in diameter. Our tube benders take advantage of ‘All-Electric’ technology thanks to which they guarantee high repeatability and fast production changes. Simple to program, they can correct the tube’s elongation and springback during bending. In addition, they offer a real advantage in terms of production flexibility by being able to produce the first piece right at each production change.
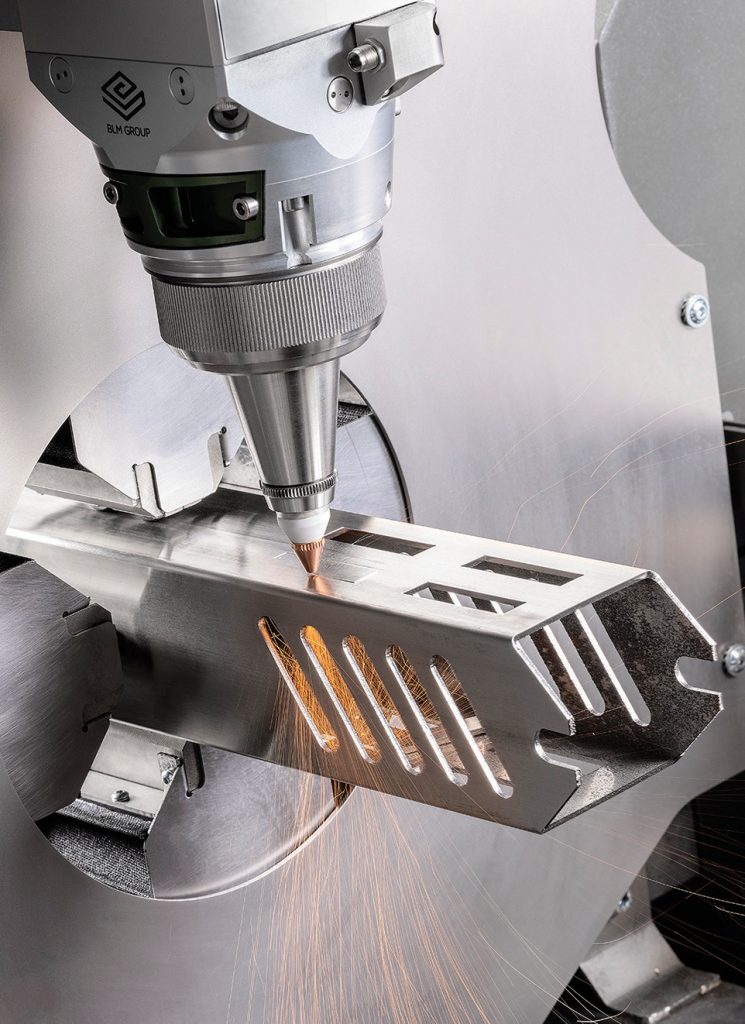
Sawing: Our cutting systems integrate all the processing required for tube, solid, and profile machining and can be supplemented with fully automatic post-cutting solutions such as brushing, washing, measuring, and ordered collection.
Tube end-forming: They can be equipped with punches, rotary tools, and trimming or rolling systems that enable a wide variety of machining operations on straight or already bent pipes. These machines can create complex shapes while preserving the characteristics of the tube, without the necessity of welding two tubes together to create complex shapes.
Wire bending: Bending does not stop at tubes, but also expands to the wire, where we find single and doubleheaded machines capable of making complex shapes on parts of any length and machining not only from coil but also bars, plates, and armored resistors.
TPI: Being dedicated to developing, designing, manufacturing, and digitizing systems; please describe your focus on bringing value-creation to the tube & pipe industry through your technological solutions.
MT: All our machines are integrated with state-of-theart programming software, and each function has been developed with our customer’s needs in mind: ease of use, interconnected machines, complex machining, and optimized management of their fleet. But there’s more! The machine-software integration allows the machines to be more efficient, for instance, by calculating in advance all the compensations to correct the effects that the tube will undergo in the different processing stages.
“Investing in research & development is vital for us because it allows us to stay one step ahead and bring more innovations to the market. We have done this in the past with the ‘All-In-One’ – a single point of management for the entire production process, for all tube processing.”
TPI: In what ways do you think industry 4.0 impacts the tube manufacturing industry with respect to innovation and achieving efficiency and productivity?
MT: Industry 4.0 is marking a turning point in the way machines are designed and used. For example, through our ProTube software, it is possible to create work programs in a single terminal and then distribute them to the various machines, or to manage production batches of various machines with greater freedom, moving them from one machine to another according to priorities.
The interconnection between machines and the client’s servers allows them to remotely monitor the progress of production batches and estimate production times. These are all functions that help our customers to have a complete overview of their plants.
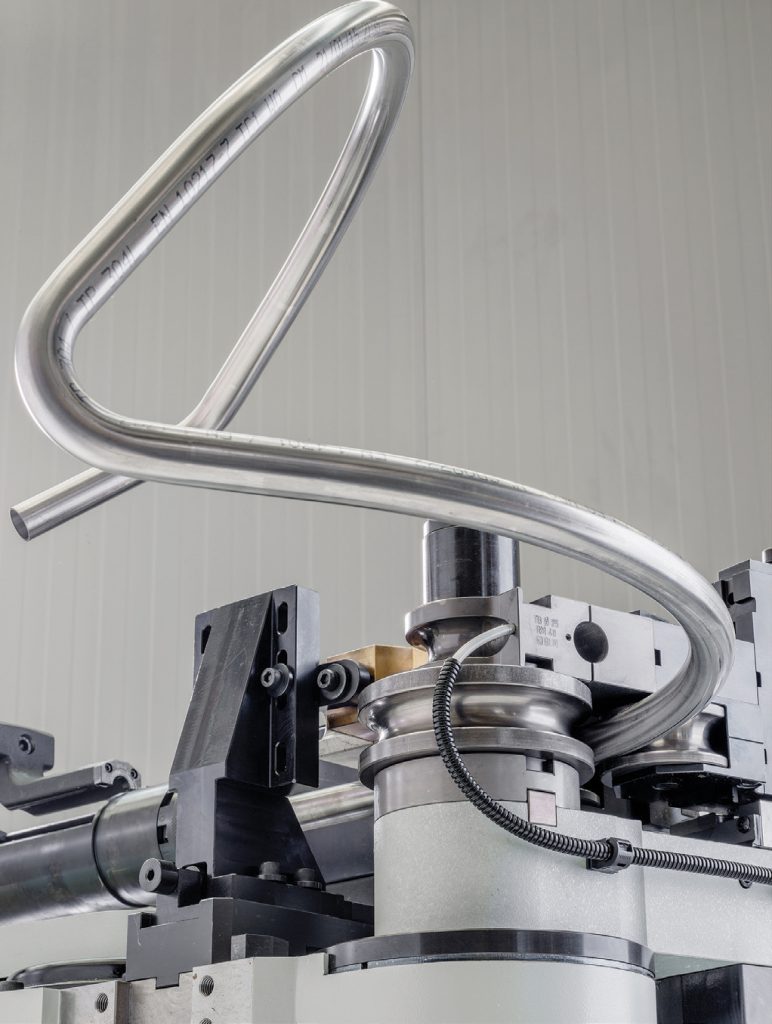
TPI: Since manufacturing innovation is contingent on R&D, how do you view the significance of investing in this area to enhance the competitive advantage of a high-tech solution provider?
MT: Investing in research & development is vital for us because it allows us to stay one step ahead and bring more innovations to the market. We have done this in the past with the ‘All-In-One’ – a single point of management for the entire production process, for all tube processing. This reduces waiting time because the tube does not have to travel from one machine to another to get to the final processing. Every year we are implementing new functions, both for the machines and for the software, so we can meet even the most special requests that come in from our customers.
TPI: Please outline your views on the tube & pipe industry and the key trends which are driving the growth of this industry.
MT: There are many factors that are contributing to the growth of the tube & pipe industry, but the main remains cost benefit. In fact, steel tubes/pipes are increasingly gaining ground in various industries (from agricultural to structural) due to their strength, durability, and reduced production costs.
In the past, other types of material were preferred because pipe processing was slow and full of intermediate processes. It required several manual machines that produced semi-finished products to be handled or stored. This increased the cost of the finished product.
Also Read: KPT Piping System to Come Up with a New Plant
Bending, cutting, drilling, and beveling – just think how long it takes to complete all these processes and transport the tube from one machine to another! Now many of these operations can be done in the same machine, such as our Lasertubes, where you can cut, drill, and bevel the tube in the same machine. All automatically!
TPI: What is your outlook on the Indian market and your future plans?
MT: We have a solid presence in the Indian market, with customers that focus on high-end solutions because of the quality of processing of our machines, especially Lasertubes and tube bending machines. In the coming years, we expect that as the demand for quality products increases, more clients will demand our machines, as we have already seen happen in other markets.