As India ramps up its exploration activities in the oil and gas sector, Maharashtra Seamless Ltd. (MSL), the flagship company of the diversified D.P. Jindal Group, has been able to develop subsea pipes in-house in its continuous efforts to manufacture import substitution products.
“We have invested to establish new laboratories for special testing facilities such as HIC and SSC and acquired a new state-of-the-art mill at Hyderabad having a capacity of 3.0 lakhs MT to roll critical pipes such as subsea pipes.”
The company recently received its first order from the Oil and Natural Gas Corporation (ONGC). In an Interview with Tube & Pipe India, Mr. Shiv Kumar Singhal, President (Commercial), Maharashtra Seamless Ltd. shares interesting details about the project.
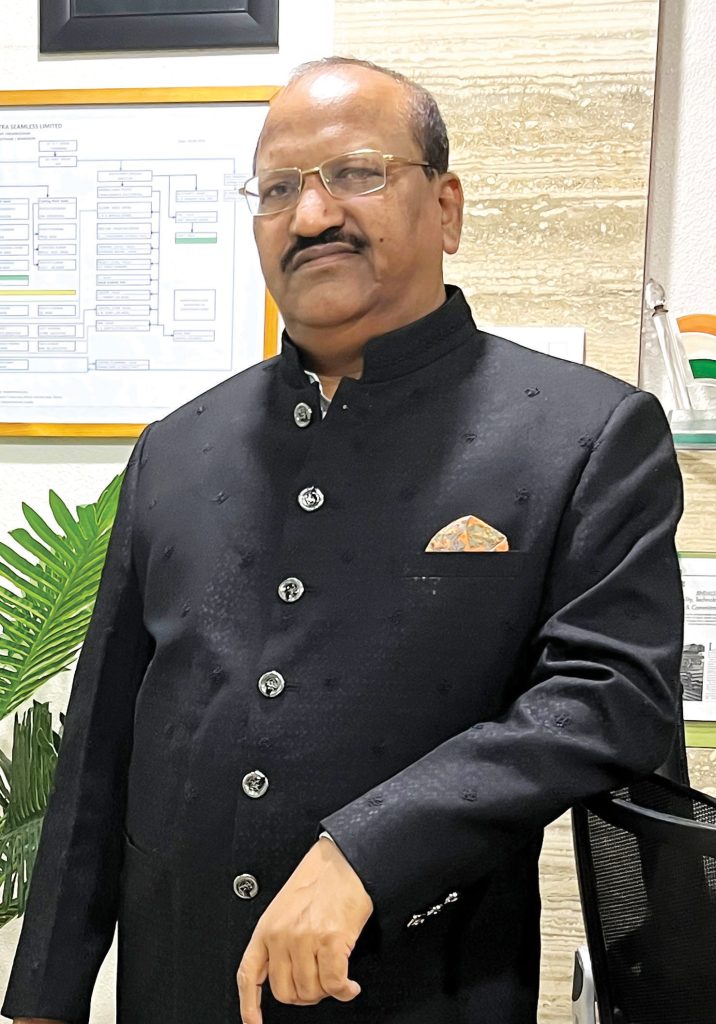
Tube & Pipe India: MSL has received its first order for a subsea pipeline in India. Tell us more about this prestigious project. What opportunities do schemes like ‘Make in India’ provide for such projects?
Shiv Kumar Singhal: The government had already spent a huge amount on imports but now India is on its way to becoming self-sufficient. DP Jindal Group has been manufacturing seamless pipes and tubes since 1992 under its flagship company Maharashtra Seamless Ltd. (MSL). We started our journey with manufacturing pipes of up to 7-inch OD. In the year 2004, we expanded and extended our range to up to 14-inch OD and now, we are manufacturing up to 20-inch OD. Maharashtra Seamless is catering to various segments & applications such as oil & gas, petrochemicals, chemical, power, boiler, construction, automotive, mechanical engineering, farming equipment, transporting waste solutions, irrigation and many more.
However, our presence was lacking in one application i.e. subsea pipeline which is the most stringent application in the oil and gas sector. We approached ONGC Ltd., a government-run organization, with our interest to develop this stringent product. With the help of their guidance, we have updated our mills and testing facilities by investing heavily to fulfill our vision of ‘Make in India’. We have not only improved at our end but also, developed the source of our raw materials domestically through the guidance of ONGC.
Later on, we submitted reports of these products to ONGC and they were satisfied and found their solution in our product as an import substitute and approved us as a vendor in the ‘Make in India’ scheme. The government has given us an opportunity to supply these subsea pipelines under ‘Make in India’ and now, we have started executing the order awarded to us. The first consignment has already been delivered satisfactorily this year.
TPI: What are the challenges of subsea pipeline development and how do you plan to address them?
SKS: Although Maharashtra Seamless has 30 years of experience in manufacturing seamless pipes, subsea pipelines are the most stringent considering application and huge costs of laying and maintenance. We have been called by ONGC officials on multiple occasions to alert us and remind us about the importance of maintaining the quality of each pipe during our development phase. Even after placing the order with the contractor, ONGC had on deputed their own inspection agencies to witness 100% during the manufacturing stage wise from raw materials to final product with zero tolerance. We have successfully supplied part quantity to ONGC in the last three months.
However, we are facing the challenges of production loss to maintain such quality and online inspection by several agencies. We have invested to establish new laboratories for special testing facilities such as HIC and SSC. We have also acquired a new state-of-the-art mill in Hyderabad having a capacity of 3.0 lakhs MT to roll critical pipes such as subsea pipes, gas cylinder pipes, casing pipes, boiler tubes and high-grade alloy steel pipes.
“We are coming up with cold drawing facilities by which we can cater to bearing, automobile and mechanical tube & pipe segments.”
TPI: Maharashtra Seamless has successfully developed manufacturing facilities for gas cylinder pipes in its subsidiary (USTPL). Tell us more about the infrastructure and R&D efforts put towards product development.
SKS: The manufacturing facilities at USTPL will play a very important role in import substitution. USTPL seamless mill is a state-of-the-art, modern FQM plant supplied by Danieli Group, Italy. It is one of the world’s best technology automated mills and produces the finest surface quality with less eccentricity, ovality, close control of dimensions and thin wall thicknesses of 6 mm. Gas cylinder pipes generally require defect-free smooth ID/OD surfaces and very close control of wall thicknesses.
TPI: Could you please outline the details of the merger of MSL & USTPL? How has this merger proven fruitful in solidifying your position in the global market?
SKS: Consolidating assets of both manufacturing units, with an eye toward stimulating growth, the merger helped us gain competitive advantages by increasing market share, and influencing supply chains. MSL has a strong brand value and USTPL has the latest technology; the merger will further help us to cater to the ‘monopolistic import market’ of gas cylinder pipes. Domestic cylinder manufacturers will save a huge amount of foreign exchange after getting state-of-the-art technology of USTPL and brand assurance of MSL (The D P Jindal Group). It would open avenues for our cylinder pipes in the export market. We can establish ourselves as a complete piping solution in the domestic as well as international markets. With a full range of seamless and ERW pipes (0.5-inch to 20-inch) under one umbrella, we can satisfy the requirements of our domestic and global customers by supplying from both plants.
TPI: What will be your strategies for serving the needs of the tube & pipe market in the country and what more can we hope to see from Maharashtra Seamless in the future ahead?
SKS: Our management has declared new investment to utilize our maximum capacity to upgrade the existing facilities and develop products for new markets. We are coming up with cold drawing facilities by which we can cater to bearing, automobile and mechanical tube & pipe segments. We can serve our customers with faster delivery of a full range of pipes, by adding more finishing lines, and testing lines in all sectors of the domestic and international market.
Also Read: Maharashtra Seamless: Aiming for Full-Capacity Utilisation & Expanding Value-Added Products
TPI: What is the success mantra behind your growth?
SKS: We have developed ourselves as per the demand of the industry. Development and innovation are the keys to leadership in the industry. Our experimental technical team and commercial team are the key strength of our success. Maharashtra Seamless has total solutions under one roof including a wide range of seamless pipes, ERW Pipes, 3-layer coating pipes, GI pipes, casing pipes, tubing, drill pipes, etc.