transfluid® is one of the leading manufacturers of tube processing machines and tube bending machines. The company offers tailor-made solutions – for plant and mechanical engineering, the automotive and energy industries, shipbuilding, aerospace, and manufacturers of medical devices.
In a conversation with Tubes & Pipes India, Mr. Simon Müller, Sales Manager, transfluid®, talks about the company’s manufacturing capabilities, product range, and new developments.
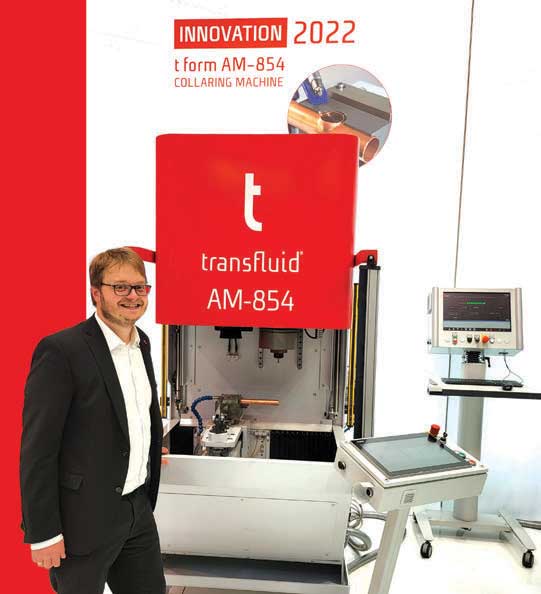
“We have developed a robot bending solution. The advantage of this robot bending machine is that you can process small dimensions such as 6mm, 8mm, and 10mm tubes with fewer vibrations in the bending process.”
Tubes & Pipes India: Please tell us about your company.
Simon Müller: transfluid® was founded in 1988. We are a company with about 230 employees. An internationally preferred partner for the production of pipe machining and bending machines – transfluid® has been developing pipe machining technologies in a customer-centric manner. We undertake the complete construction, designing, and manufacturing of tube bending, tube forming, tube cutting lines, and also fully automated systems. We provide turnkey solutions to our customers.
TPI: Tell us a bit about your manufacturing capabilities.
SM: We are manufacturing about 250 machines per year for various applications in different sectors. transfluid® offers tailor-made solutions for applications ranging from plant and mechanical engineering, automotive & energy industries, shipbuilding, and aerospace to the production of medical equipment. The engineering is mostly done in Germany. We have a lot of companies who are sub- supplying us, but we have the possibilities to manufacture main components such as tooling. We do a lot of design and development for our customers.
TPI: Could you shed some light on the product range of transfluid®?
SM: We have bending machines for tube diameters from 4 mm up to 330 mm. The tube of a bigger diameter is used in the shipbuilding and offshore industry, whereas the smaller sizes are used in the automotive industry for heating applications. We have cutting machines, Chipless orbital cutting systems, and Knife cutting for the range up to 120 mm. The biggest advantage of the Chipless orbital cutting system is that you don’t have to clean the tubes after cutting as unlike saw cutting, there are no chips produced. The tubes can directly be used in further processing steps.
We have a tailor-made answer to the challenges of tube and tube end forming: tight tolerances, sharp edge contours, polished surfaces, and the processing of high- strength materials are converted into an almost unlimited variety of forms with the greatest precision possible.
Our machines, with different equipment and electrical or hydraulic forming axes create limitless possibilities for the accurate and fast realisation of the most diverse forms.
TPI: What are the key strengths of your company?
SM: In my opinion, flexibility is the key strength of our company. We are doing a lot of customisations for our customers to make sure that they get the desired results from our machines. We customise our standup machines to provide benefits to customers. After taking a look at the customer needs and the application of the products they intend to manufacture, we assess the different courses of action on what we can do to get our machines running in the best possible ways for our customers, besides being economical.
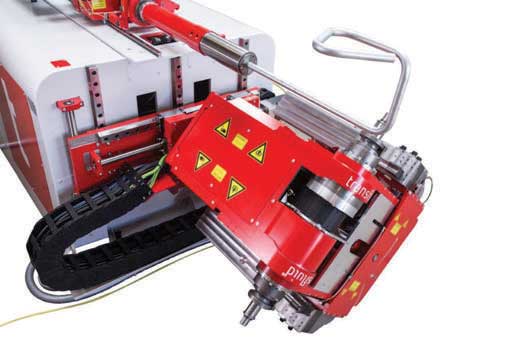
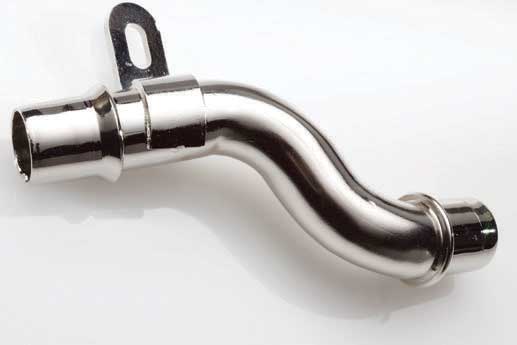
TPI: Tell us about your presence in the Indian market.
SM: We have a partner in India, Fortec and they are the exclusive reseller of transfluid® for more than 10 years. They have their own service on-site so that they can do the maintenance on our machines or help our customers with the installation of the machines. However, we are also doing a lot of services directly from Germany, especially if we have big, fully-automated production lines delivered to India. We help them get the machines running and conduct proper training.
Over the years, we have had various machines in India including 50 different types of newer ones and a lot of them include auto loading and unloading functions. We have many hand-operated machines as well as automated systems.
TPI: Has there been any recent development in transfluid®?
SM: At transfluid®, we have put a lot of work into the development of our type SRM forming machines. We use the rolling method to optimise the collaring process for tubes. We have also developed a robot bending solution. The advantage of this robot bending machine is that you can process small dimensions such as 6mm, 8mm, and 10mm tubes with fewer vibrations in the bending process. It can take the tube, bend the tube, and unload the tube. It is quite an economical solution as you don’t need to be a robot programmer to handle the machine. One would be able to run this machine after about half a day of training on the transfluid® bend software.
Also Read: Crippa: Innovative Technological Solutions in Response to Dynamic Market Demands
TPI: What are the future plans of your company?
SM: In the near future, we would consider e-mobility and for our first project; we are bending busbars for electric cars. We are looking for new businesses and new industries which are processing tubes. There are a lot of new things starting up every year.