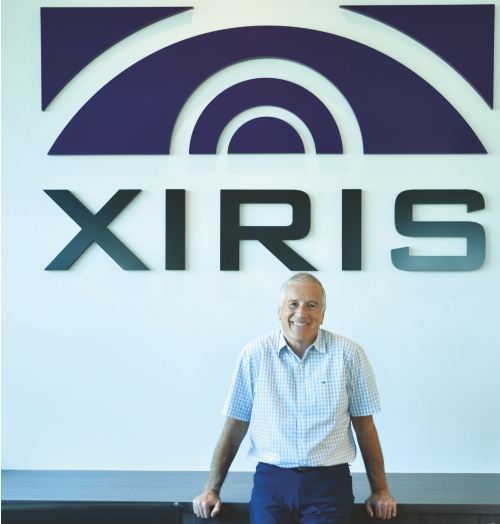
Xiris Automation Inc. is involved in the research, development, and manufacture of high-technology machine vision products requiring a multidisciplinary staff that includes software, mechanical, electrical, and optical engineering skills. They have been developing specialized machine vision products for process & quality control for over 30 years. The company employs highly skilled engineers, computer scientists, and technicians who are all involved in the design and development of machine vision systems and software. They design and manufacture all their products internally at their head office in Canada with about 43 staff. In addition, they have a European sales and service office in Germany and a sales office in Thailand. In a recent interaction with Tube & Pipe India, Mr. Cameron Serles, Founder and CEO, Xiris Automation Inc., shared the history of the company, product portfolio, recent developments, and plans for the future with respect to the Indian market.
Tube & Pipe India: Please tell us about your company and its history.
Cameron Serles: Xiris Automation Inc. was originally founded in 1989 to build custom machine vision solutions. Over the years, the company has developed a variety of machine vision systems for the automotive, pharmaceutical, semiconductor, electronics, and plastics industries. However, developing custom machine vision systems is a difficult business model, so in the early 2000s, Xiris started looking for a growing market that was in need of standard machine vision products, one where Xiris could bring its expertise and engineering capabilities to create superior solutions. After making several false starts, we finally settled on the metalworking industry, thinking that it offered a number of interesting opportunities for camera systems. In about 2008, Xiris discovered the tube and pipe market, learning that a need existed to develop a camera system to measure the weld bead profile of a tube right after the weld box to detect quality defects in the weld and the forming of the tube. An intensive development effort ensued where we designed a brand new product platform, bringing it to market in about 2011. It was a category in itself, as there were no significant competitors, so we had to teach the industry the value of such technology. At first, the adoption rate was slow as our limited resources could not reach too many customers. But after a few years, it did pick up pace as we started expanding our sales channel. Now, we have sold almost 300 weld inspection systems worldwide to the tube and pipe industry.
With constant R&D, we came out with a product line of HDR weld cameras that can be used in various welding applications to see the weld arc, the weld torch, and surrounding environment in 2013 or so. It was an instant hit and its use spread rapidly across the welding industry, including applications in the tube industry to look at TIG, laser, or plasma torches while they are operating. That development was followed by the development of a short-wave infrared (SWIR) thermal camera that can look at welding processes and measure the temperature of hot metals in the range of 350-1800°C, allowing process engineers to do advanced quality control of their welding processes by accurately measuring the size of the melt pool, the T8/5 cooling rate of the weld bead and other process variables. All our cameras connect to a PC that is used for camera controls, recording and playback of video, graphical feedback tools, and machine vision algorithms to extract data from the images.
Today, Xiris Automation Inc. is involved in the research, development, and manufacture of high-technology machine vision products requiring a multidisciplinary staff that includes software, mechanical, electrical, and optical engineering skills. The company employs highly skilled engineers, computer scientists, and technicians who are all involved in the design and development of machine vision systems and software.
TPI: Cast some light on the infrastructure setup at your facility.
CS: We design and manufacture all our products internally at our head office in Canada with about 43 staff. In addition, we have a European sales and service office in Germany and a sales office in Thailand. We have an R&D team of about 13 people that comprises optical, mechanical, electronic, and software engineers and technicians. We also have a full in-house production facility that is equipped to assemble, calibrate, and test all our products before they get shipped. As a result, we are rather unique in the industry where we both develop all our own technology and build it in-house, including our software, so that we can respond quickly to market trends and release new products. Our goal is to develop 2-4 new products per year plus release new versions of our software every 3 months.
TPI: Kindly shed some light on your product portfolio and major clientele.
CS: Our product portfolio for the tube and pipe industry centers around two main technologies: laser triangulation as used by our WI2200/3000 post-weld inspection product line to measure the weld bead and forming geometry of welded tubes and pipes; and SWIR thermal imaging technology in our XIR-1800 camera that is used to acquire 2D thermal images of hot metal and use them for thermography (measuring temperatures) or enhance machine vision.
The WI-2200/3000 post-weld inspection system detects quality issues related to the forming, welding, and scarfing processes on a tube or pipe mill. By using this system to measure key variables such as mismatch, undercut, sunken weld bead, freeze line, roll, and others, tube producers take the first step in controlling them and improving weld quality. Xiris’ proven laser-based vision system technology uses high-resolution imaging, fast data capture, and analysis rates to provide real-time detection of defects. The system can be a single or double-head configuration, to monitor post-weld and/or post-scarf processes.
The XIR-1800 is a high dynamic range (HDR) SWIR thermal camera designed for use in critical metal joining and additive manufacturing applications where the thermal properties of key features need to be carefully monitored in real-time. Combining a spectacular 120+ dB HDR capability with sensitivity to the short-wave infrared (SWIR) spectrum, the XIR-1800 thermal camera provides enhanced imaging of metal joining processes beyond what is visible using standard thermal or visible-light cameras. Because it is based on SWIR imaging, the camera is able to image through smoke or fumes to provide exceptionally clear, real-time views of any metal melting process.
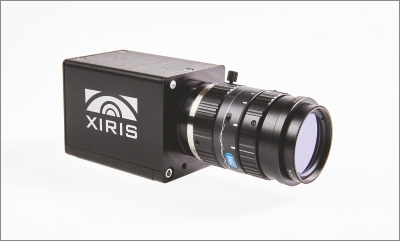
Most recently, we have created a new product; our HF pre-weld inspection system that enables operators to remotely monitor the welding process inside the weld area of high-frequency tube mills. Using thermal video, the HF pre-weld inspection system provides a real-time view of the welding process and uses advanced software to measure, monitor, and record process parameters such as V angle, V length, seam gap, hotpoint, and various other parameters. Automated deviation monitoring and defect marking using these measures enables mill operators to enhance tube welding quality and achieve optimal production results. We also have a vision system for TIG, plasma, and laser tube mill operators. This solution provides a leading-edge view of the torch and gap, with automated feature extraction software used to monitor alignment offsets and/or gap measurements. A clear view of the torch condition and melt pool allows operators to react quickly to problems. Alignment offsets are also available for output to external torch positioners – allowing real-time automated re-alignment.
Our client list includes ArcelorMittal, TATA Steel, Sanoh, Tenneco, Tenaris, Fischer, Nucor, Stala Tube, Sankei, Nippon Steel, Schoeller, TERNI, Prolamsa, Siemens, GM, Caterpillar, Magna, Alstom, BMW, Hitachi, ThyssenKrupp, HP, Abicor Binzel, Lincoln Electric, Miller, Airgas, etc. and many more.
TPI: What is your USP? How does the company stay ahead of the competition?
CS: Our products all have a common USP: they are high-technology, high-value solutions that reliably gather information about the welding process that is not readily available in a competitive product. We have a unique ability to deliver a combination of advanced hardware based on mechanical, electronic, and optical engineering as well as advanced machine vision software engineering. Our products are highly focused to the industries we serve, such as the tube and pipe industry, where we spend a great deal of time understanding the problems being experienced by our customers before we develop our solutions to meet the industry’s needs.
Also Read: HYPREX: Japan’s Leading High- Pressure Fabrication & Testing Technology Supplier
TPI: Could you tell us about recent & noteworthy projects accomplished by your company?
CS: Monitoring the HF tube welding process is challenging and dangerous. To improve safety for its operation staff and get a clear, close-up view of the weld ‘V’, a major North American pipe producer came to Xiris for a solution. They required a remote monitoring solution to observe and automatically warn of deviations in certain mechanical variations in their HF process, namely:
- Breathing on the V gap, or the cyclical instability of the tube of the space between the two strip edges just after the induction coil. Such a phenomenon could be the result of imperfect forming rollers, varying stresses along the pipe, or variances in the heat going into the tube;
- Position of the weld apex as it relates to the weld squeeze point. The weld apex is defined to be the point on the tube where the two strip edges of the tube come together and first touch. Its location is a result of a number of factors including the V angle, the forming roll position, and pressure and inductive energy flowing into the pipe;
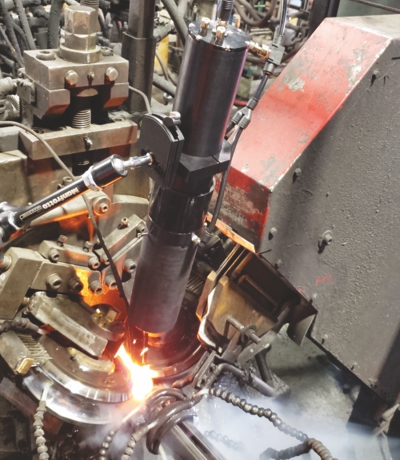
For this application, we developed our HF pre-weld inspection system, based on our Xiris XIR-1800 HDR SWIR thermal camera encased in a specially designed housing and placed at the HF weld environment to look at the weld ‘V’ immediately after the induction coil. The housing provides controlled airflow to ensure that no steam, smoke, or other particulates can reach the camera optics and interfere with the image.
Process-tailored software tools ensure that the weld operator can detect the weld apex and any breathing that could occur in the seam gap on the pipe. The goal of giving the operator real-time measurable process feedback with working range limit alarm notifications was achieved so that the mill can process any anomalies and/or defects accordingly. Integrations to paint and laser marking tools were added by the customer. What started as a safety initiative resulted in a significant process improvement solution: the producer was able to achieve higher yields from a more stable process, delivered with a safer approach to monitoring the weld process, reducing the potential for operator injury.
TPI: Do you undertake R&D at your company? How do you maintain the quality of your offerings?
CS: As identified above, we are constantly developing new technology. We call it “Innovation Kaizen” based on the Japanese approach of designing for the better. Our goal is to always improve everything we do, not just our products, but also how they operate, how we operate as a company, and deal with our customers. Our goal of developing 2-4 new products per year pushes us to always think about developing new and better products.
TPI: What are your vision and plans for your company’s future? Do you have any specific plans for the Indian market?
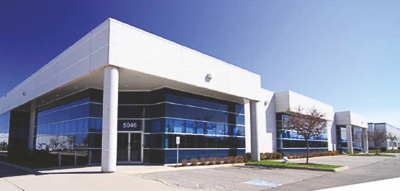
CS: We are very excited about our recent entry into the Indian market. We feel that we are in the early stages of a boom as the pipe and tube market in India seems to be poised for spectacular growth over the next few years. We have made initial sales of our weld inspection and HF pre-weld inspection systems to key Indian brands with great success. We look forward to extending our partnership with these pre-eminent tube makers to convert them to repeat buyers of our equipment as well as expanding to the rest of the India tube industry. In 2022, we received our BIS certification for our specialty vision sensors. We hope to continue to grow our Indian business, eventually opening a sales and service office in India one day.
To consolidate our recent successes, we are exhibiting at the upcoming Tube & Pipe Fair – India show in New Delhi.