Started in 1977, InspecTech Analygas has been a leader in customizingNon-destructive testing (NDT) solutions for their clients present all over the world. InspecTech owns 50 percent of the market share of the NDT business in the U.S. and 80 percent of the market share of the NDT business in Mexico. For fifteen years, InspecTech designed and supplied sophisticated in-service inspection pigs that use the flux leakage technique to gather high-resolution data from oil and gas transmission pipelines. The revolution in digital technology has closely tracked InspecTech’s own history and the effects have been remarkable. Today, in addition to their in-house electrical and mechanical engineers, the company has software and firmware specialists, and all information technology functions are customized to their systems and to their client’s own needs.
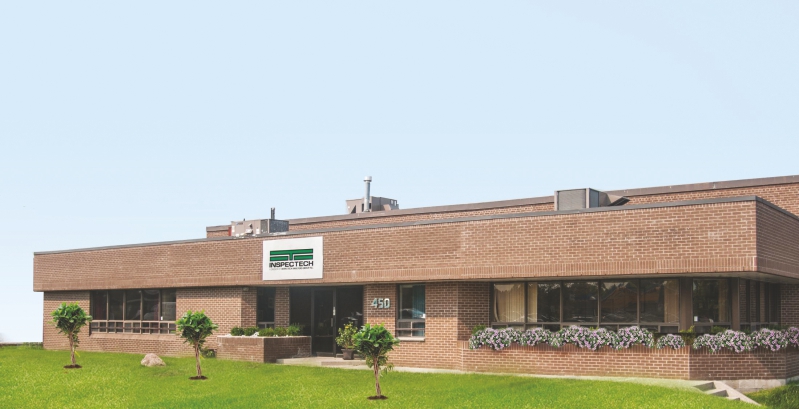
Overview of the Company and Crucial Milestones
InspecTech has been in business since 1977 customizing NDT solutions utilizing the eddy current, flux leakage, and ultrasonic technologies. We take a look at your application, and which specifications you need to meet and then recommend the best technology. InspecTech’s objective is to supply engineered solutions to NDT problems by providing innovative and rugged test systems, fully integrated into the production environment. InspecTech manufactures all mechanics, and electronics, and develops our own software in-house. For fifteen years, InspecTech designed and supplied sophisticated in-service inspection pigs that use the flux leakage technique to gather high-resolution data from oil and gas transmission pipelines. Our major accomplishments include a compressed gas cylinder testing unit, the first in North America for a production environment in continuous use since 1992. InspecTech pioneered the use of flux leakage testing for welded tubes and is a leader in the field. Flux leakage test systems for use on laser-welded automotive panel blanks were also pioneered by InspecTech and are in use in Europe, China, and the USA. Ultrasonic test systems for the welded tube industry include ERW, DSA long seam, and spiral welded products in use worldwide. Semi-automated ring gear test systems for automotive parts, in mass production use since 1993. Multi-probe thread detection and evaluation systems.
Industries Catered and Market Footprint
Currently, Inspectech is present in the oil and gas industry, automotive industry, and we also provide structural and turnkey solutions. InspecTech owns 50% of the market share of the NDT business in the U.S. and 80% of the market share of the NDT business in Mexico. InspecTech added 7 new representatives in South America, Europe as well as Chengdu, China. Our global network is spread across the globe including Asia Pacific, Canada, Europe, Latin America, Russia, South America, United States. Some of our major clients are Tenaris, Tejas, Peasa, Tenneco, Chung-Hung Steel, American Cast Iron Co., Forza, Canadian Phoenix, Thyssenkrupp, etc.
Product Portfolio
We have a diverse range of products in our product portfolio. Eddy current full body, Eddy current weld line, offline and online ultrasonic testing, and ultrasonic skelp monitoring system are some of the products.
IBIS SCARF MONITORING SYSTEM
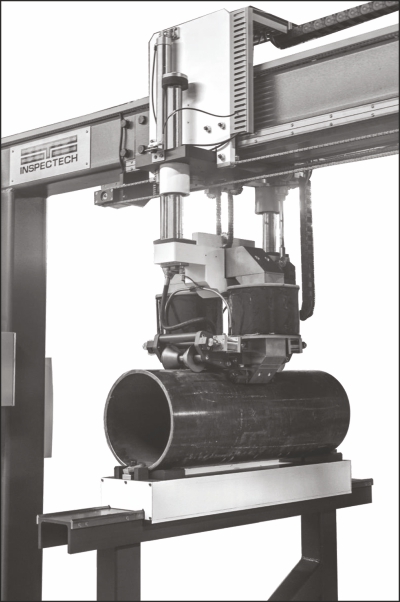
The InspecTech® I.B.I.S. (InspecTech B-Scan Inspection System) is an ultrasonic device that is especially useful to the welded tube industry. The I.B.I.S. scans the weld zone and monitors the quality of the flash removal process. Its key features are-
- Scrap Reduction- Catch flash removal problems before they become costly.
- Real-time presentation of wall thickness data in engineering units over the weld.
- Audio and visual alarms for high and low limits of wall thickness.
- “Hands Free” unattended operation.
- Complete Data Logging of all online test parameters easily stored, retrieved, hard-copied or downloaded.
- Instant recall of previously used setups.
- Weight calculation and cutting to weight (optional).
The I.B.I.S. is primarily a scrap reduction tool. It displays the weld profile in engineering units and in real-time on a video display. Broken, worn, or chipped flash-cutting tools or mismatched weld edges are easily detected and alarmed. The I.B.I.S. will also monitor the weld profile to make sure that the overall weld thickness is within tolerance.
MAGNETIC FLUX LEAKAGE SYSTEM
While the Magnetic Flux Leakage (MFL) method is one of the oldest NDT methods, its utilization to test laser weld seams in carbon steel tailored blanks is relatively new. The simplicity of setup and high sensitivity make the method a superior alternative in an industry previously dominated by ultrasonic EMATs and eddy current testers. The standard MFL package offered by InspecTech can test welded steel blanks up to 3mm thick. Testing is done by passing the material seam over the test head on a conveyor, or by passing the test head over the part by robotic manipulation. Its key features are-
- Inspect laser welded seams in carbon steel plates, online, at high speeds.
- Absolute and differential channels differentiate between short and long defects.
- Ideal NDT for carbon steel plates up to 3 mm in thickness.
- Programmable set-up and changeover between products.
- Storage of all test results based on time, or piece by piece basis.
- Calibrates on 10% OD and ID notches and 0.5 mm holes.
- Economical and user-friendly.
The typical location for the MFL system can be directly after the welder on the welding line, or at a downstream handling station for the welded product. There is also a special version of the MFL system designed for use on a continuous welding line. It has a marking system to spray defects and a modified machine interface.
Also Read: Xiris Automation: Solutions for Weld Inspection and Monitoring
ON-LINE ULTRASONIC TESTING SYSTEM SPIRAL
Over the years the welded tube industry has come to rely on InspecTech® ultrasonic testing systems to verify weld quality and integrity both on the tube mill and on the finishing floor. Ultrasonic testing of welded tubes is a universally recognized method, offering equal sensitivity to both inside and outside defects regardless of material thickness. Codes of practice such as ISO, API, and CSA all cite ultrasonic testing of welds as an acceptable, or even mandatory, method. Depending upon the requirement, InspecTech can supply systems with 2, 4, 6, or more transducers to test various material thickness ranges and also to test HAZ (heat-affected zones) and monitor material gauges. Its key features are-
- Advanced transducer technology.
- Multi-probe test heads are easy to set up and calibrate.
- Ideal for inspecting API-5L, API-5CT, and ISO standards.
- Robust mechanical construction.
- Complete data logging of all online test parameter data is easily stored, retrieved, hard-copied, or downloaded.
- Instant recall of previously used setups.
With many years of experience in NDT systems, InspecTech exercises continuous improvement policies, to supply the welded tube industry with systems of the highest reliability and sophistication, coupled with ease of understanding and operation. For weld-line testing of carbon steel tubing 50mm (2.0”) in diameter and up (and more recently down to much smaller diameters), the method of choice is ultrasonic testing. Ultrasonic testing is very sensitive to defects throughout the weld section and, at the same time, the test is relatively insensitive to process variations.
Research and Development
InspecTech’s research and development team works closely with our clients, towards a goal of continuous improvement to our equipment and systems. For example, the use of Flux Leakage testing for ERW long seams is rapidly gaining international acceptance.