The new EAF will significantly contribute to the Stahl-Holding Saar (SHS) carbon neutrality plan by 2045 under the Power4Steel initiative. The cutting-edge automation will ensure enhanced operational efficiency and safety. With 300 MVA of transformer capacity it is one of the strongest EAF worldwide.
Oct 14, 2024
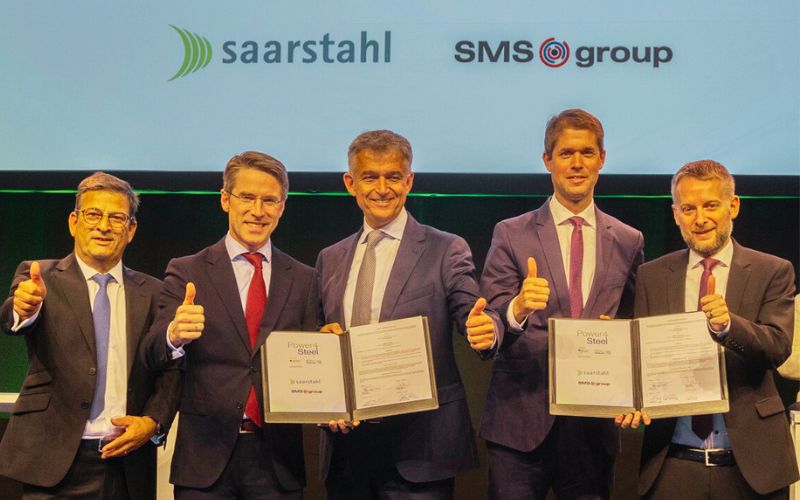
SMS group was awarded a contract to supply one of the world’s strongest Alternate Current-Electric Arc Furnaces (AC-EAF) and its auxiliaries to Saarstahl in Völklingen, Germany. This will contribute to SHS’ goal to achieve carbon neutrality by 2045. The new 185-tons EAF will be built within an already defined brownfield area. With a transformer capacity of 300 MVA, it will be one of the strongest EAF in the world. Additionally, it will process a flexible mix of up to 100 percent scrap or 80 percent Cold Direct Reduced Iron (CDRI)/ Hot Briquetted Iron (HBI) and 20 percent scrap.
Featuring 9.3-meter shell-diameter – the largest EAF ever built by SMS group – it will have an annual capacity of 1.9 million tons of liquid steel. This investment aligns with SHS’s strategic plan to utilize a mix of 70-85 percent natural gas and 30-15 percent hydrogen as an energy source by 2030, significantly reducing carbon emissions.
Jochen Burg, CEO SMS group: “We are proud to play a key role in Europe’s green steel transformation with this major project for Saarstahl and SHS – Stahl-Holding Saar. The project highlights the long-standing partnership between SHS and SMS group. With an installed power of 300 MVA the new EAF is the biggest ever built by SMS group and will set a new milestone in a carbon-neutral future for the steel industry in Europe.”
With phase I starting in October 2024 and the first heat expected in September 2028, the plant will produce various steel grades, including bearing steel, free-cutting steel, and spring steel. The EAF will be equipped with Condoor®, SMS’ enhanced slag door, ensuring significant advantages in terms of safety, productivity, energy savings and environmental impact. Condoor® enables automatic operation, reduces power-off time, ensures a clean slag door sill, saves energy and lowers NOx emissions with a sealed shell. Additionally, it optimizes slag residence time, improving flux and raw material use while reducing electrode, carbon and lime consumption, thus lowering CO2 footprint.
Also Read: Viraj Profiles Forays Into Seamless Pipe Market with the Inauguration of New Mill
Part of the scope is also a material handling system with bins designed for specific production grades, a liquid steel handling, refractory repair area, a water treatment plant, compressed air piping, two fume treatment plants, energy recovery and electric/automation systems, noise insulation, hybrid technology cars for scrap bucket movements, auxiliary cranes as well as bay and field piping. The EAF will feature SMS group’s advanced X-Pact® automation, including X-Pact® Sense for leakage detection and X-Pact® Autotap for safe and automated tapping. Genius CM® will be implemented for predictive maintenance, enhancing operational efficiency and safety. Additional innovations include SafEBT-clean for automatic cleaning of the Eccentric Bottom Tapping (EBT) channel to ensure the highest rate of spontaneous EBT opening, SafEBT-fill for automatic sand filling, temperature taking and exchange of probes.