Keeping the vision of “Make in India”, Arora Technologies (P) Limited is focusing on the manufacturing and distribution of NDT products & accessories. Their vision is to innovate, design, and manufacture NDT products, systems, and accessories for global markets by incorporating quality & excellence in their DNA. Their OEM Pruftechnik NDT has introduced the latest version of their Magnetic Flux Leakage Testing (MFLT) system – NOVAFLUX New Generation. The MFLT system excels in detecting cracks and adopts its rotation speed to the actual outer diameter of the testing bars.
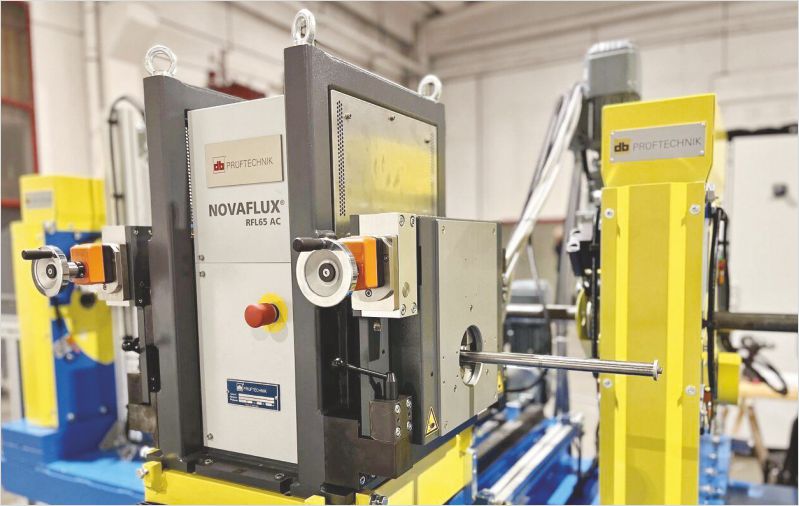
Magnetic Flux Leakage (MFL) testing stands out as a highly efficient and reliable electromagnetic nondestructive testing (NDT) method widely applied for inspecting ferromagnetic materials. Its versatility lies in its capability to detect a range of defects, including cracks, corrosion, pitting, and cavities, both on the surface and subsurface. This makes MFL testing instrumental in ensuring the integrity and safety of structures across diverse industries such as petrochemical, energy, manufacturing, and transportation.
Recognizing the industry’s needs and recognizing the advantages it brings, their esteemed OEM, M/s. Pruftechnik NDT has introduced the latest version of their Magnetic Flux Leakage Testing (MFLT) system – NOVAFLUX New Generation. After more than 20 years of field experience and 80+ installations worldwide, Pruftechnik has adopted the latest digital signal processing technology to its system capabilities. Tailored for the detection of flaws in black as well as bright metal bars, this innovative system from Pruftechnik NDT offers stable precision, ensuring reliable test results both for offline and inline testing setups.
Designed with precision in mind, the MFLT system excels in detecting cracks as small as 0.1 mm in depth and adopts its rotation speed to the actual outer diameter of the testing bars – providing a level of sensitivity crucial for maintaining the integrity of materials. The system features rotating units available in three different sizes, catering to various product diameters from 5mm to 200mm.
The principle of MFL testing is based on the interaction between magnetic field and defects. A typical MFL testing device comprises key components: a magnetizing unit, a sensing unit, a signal conditioning unit, an analog-to-digital converter (ADC), and a computer equipped with signal display and analysis software. The magnetizing unit utilizes permanent magnets or magnetizing coils to saturate or near-saturate the ferromagnetic specimen. The abrupt change in magnetic reluctance at defects causes magnetic flux to leak into the surrounding air.
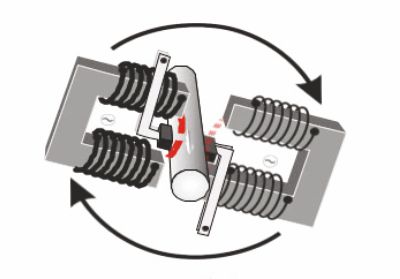
To capture this leakage, an array of magnetic field sensors records the perturbation of the magnetic field. The resulting data is then utilized to assess and quantify the identified defects. This comprehensive approach makes MFL testing an indispensable tool in the realm of nondestructive testing, contributing significantly to the maintenance of structural integrity and safety in critical industries.
The basic principle of MFL testing is schematically shown in the graphic, where a magnetizer is applied to magnetize the ferromagnetic specimen into near saturation. The magnetizer can be either a magnet with a ferromagnetic yoke or a magnetizing coil, here the yokes magnetize the test piece at a distance of a few millimeters. Special test shoes with protected probes located between the yoke arms scan the surface of the test piece by sliding over it. Due to the high permeability of ferromagnetic materials, the magnetic flux is constrained in the material when no defects are presented. In the presence of a defect, the magnetic field leaks into the nearby air and causes the leakage field. A testing system that senses the deviation and displays the reports of this deviation including exact localization information.
Also Read: Tube & Pipe Fair 2024: 2nd Edition in Hyderabad
Over the course of several decades, Magnetic Flux Leakage (MFL) testing theory and technology have undergone continuous development, proving particularly advantageous in inspecting long products such as black and bright metal bars and seamless tubes. Within the realm of evaluating inspection integrity for bars, MFL testing, alongside ultrasonic inspection techniques, has emerged as a widely adopted method. Despite the prevalence of these techniques, uncertainties persist in their results, necessitating thorough quantification and evaluation.
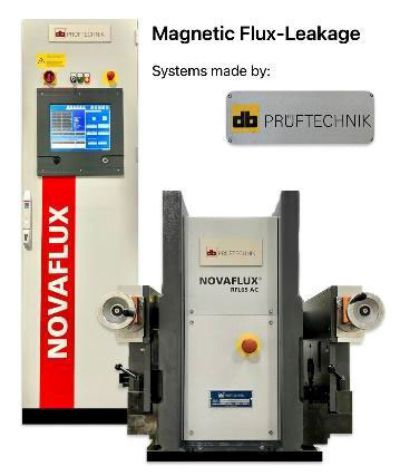
Magnetic flux leakage stands out as the predominant method, renowned for its ability to detect cracks in both axial and circumferential directions. One key advantage is its minimal need for pre-processing, with easily detectable signals. This allows for seamless offline as well as online detection, facilitating a high degree of automation. Furthermore, the method is versatile in detecting various defect types, not only on internal surfaces but also on external surfaces. The detection environment’s requirements are relatively undemanding, and the method remains unaffected by the characteristics of the transportation medium.
In conclusion, the MFLT system from Pruftechnik NDT emerges as a groundbreaking solution that not only addresses the specific needs of the industry but also stands out for its endurance and stability. Its ability to deliver reliable results makes it a valuable choice for diverse testing setups. The inherent advantages of efficiency, versatility, and broad applicability make the MFLT system a valuable asset for industries relying on precision testing for their ferromagnetic materials.