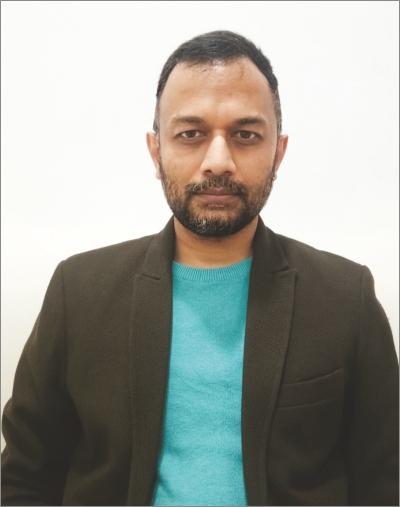
Incorporated in 1975 in Dewas, Deetee Industries has a total of three manufacturing units in Indore- the tooling division unit, RMR division unit & TMR division unit; offering a complete range of slitting line tooling, cold rolling mill rolls, tube-forming rolls, section-forming rolls etc. confirming international standards. Presently, their products are exported to over sixty-five countries all over the world including the USA, Canada, the UK, France, Australia, Germany, Korea, South Africa, Malaysia, the Gulf countries, Southeast Asian countries, etc. DeeTee uses COPRA (German) software for the roll designing which helps them to design the rolls with utmost perfection. It has been awarded a Certificate of Export Excellence by the Indian Government. DeeTee is soon coming up with a 1,50,000 square feet new facility, along with an advanced heat treatment facility and other new imported machinery. In a recent interaction with Tube & Pipe India, Mr. Aradhya Baheti, Managing Director, DeeTee Industries Private Limited, shared the company’s history, infrastructure setup, and product portfolio. He also talked about the company’s recent developments and future vision of the company.
Tube & Pipe India: Please tell us about your company’s history, significant milestones, and crucial achievements.
Aradhya Baheti: DeeTee Industries, established in 1975, has quickly grown into the biggest and leading manufacturer and exporter of international quality industrial tools from India.
Incorporated in 1975 as an ancillary unit-I, in Dewas; DeeTee started producing cold rolling mill rolls with its second unit-II in 1983, in Indore. They shipped their first export to the Gulf in 1986. Thereby in 2002, DeeTee started their 3rd unit for tube mill rolls & bar mill tooling. In 2010, DeeTee partnered with European slitter tooling manufacturer- EmmeBi-Lame Srl. Today, EmmeBi-DeeTee jointly market products in Europe.
A wide range of products are manufactured at DeeTee which include slitting line tooling, tube/section forming rolls, bar/ wire rod mill rolls, cold rolling mill rolls for 2Hi, 4Hi, 6Hi, and 20 Hi mills, Sendzimir mills rolls, leveler rolls, shear blades, tube cut off knives, friction saws, shafts, and arbors, etc. DeeTee’s products are exported to over sixty-five countries all over the world. We are now producing 12000 pcs per month of slitting line tooling and 3000 tube forming/section forming rolls per month with a maximum of dia.900 mm. We are the first in this line in India to be certified with ISO certification, and cater to about 50 percent of the requirement of such tools in the domestic market– the “largest in India”. Additionally, we have now started manufacturing extrusion tooling and bright bar tooling.
“DeeTee caters to about 50 percent of the requirement of tools in the domestic market – the “largest in India”. All steel giants in the domestic market are our customers like AMNS, JSW, Jindal, Apl Apollo, TATA Steel, etc.”
TPI: Cast some light on the infrastructure setup at your facility.
AB: DeeTee Industries has a total of three manufacturing units in Indore. In unit 1 which is the tooling division, we manufacture complete slitting line tooling, including slitting knives, spacers, over-arm separators, rubberized spacers, rubber rings, COC cutters, fins, etc. Our tooling division has an in-house heat treatment facility and we can do heat treatment of jobs up to 650 mm dia. In our Unit 2, RMR division, we manufacture cold rolling mill rolls like work rolls, and other rolls for 6Hi, 4Hi, and 2 Hi mills, Sendzimir mill rolls, backup rolls, skin pass mill rolls, flattener rolls, deflector rolls, shafts, and leveler rolls, long shear blades, extrusion tooling, bright bar tooling, etc. Here also, we have an in-house heat treatment facility, where we can do the HT process for bigger jobs and heavy weights i.e. parts diameter 550 mm (max.) and weight up to 3000 kgs (max). Unit 3 which is the TMR division, is responsible for manufacturing tube-forming rolls, section-forming rolls, bar/ wire rod mill rolls small shear blades, tube cut-off knives, etc., and here we can make tube-forming / section-forming rolls up to dia.900 mm and weight up to 3000 kgs.
TPI: Kindly shed some light on your product portfolio and its application areas.
AB: We have a diverse range of products in our product basket. DeeTee offers a complete range of slitting line tooling confirming international standards. These include rotary metal slitting knives, metal spacers, rubber-bonded spacers, stripper rings, over-arm separator discs, shims, and other precision tools. DeeTee’s slitting line tooling has the highest degree of hardness uniformity and the ideal metallurgical properties to slit any metal. DeeTee manufactures slitting line tooling in precision and extra precision tolerance grades with lapping. DeeTee can manufacture slitting line knives and spacers up to 750mm in diameter.
We also manufacture world-class forged rolls- Sendzimir mill rolls/cluster mill rolls, 6Hi, 4Hi, and 2Hi mill rolls, skin pass rolls leveler rolls and shear blades, etc. The rolls are prone to very tough working conditions and are perfect in terms of wear resistance, toughness, and hardness. Right from the raw material inspection, to heat treatment to grinding and final dispatch, all rolls undergo very stringent quality checks. We manufacture various types of rolls for all metal processing in rolling mills including tube forming rolls, rod mill rolls, tube mill tooling, wire rod mill rolls, tube mill shafts, bar mill rolls, section forming rolls, etc.
Metal processing rolls that are manufactured by DeeTee find their application in welded tubes, seamless tubes, open sections, wire rods, tube straightening, and various other industrial applications.
Tube forming and section forming roll designing is a very critical stage as it affects the cost of the rolls, the life of the rolls, the productivity of the mill, and the quality of the tube/section. DeeTee uses COPRA (German) software for the roll designing. The customer has to provide only the basic details of the mill and the input and output details, and DeeTee can design the rolls with utmost perfection. Salt bath heat treatment is considered to be the best for tool steels. The high-carbon-high-chromium grades of steel used for manufacturing tube and section forming rolls are through hardening steels i.e., when heat-treated they attain the hardness right from the outer surface till the inner core. Proper heat treatment gives good toughness, wear resistance, and uniform hardness to the rolls. The profile of the rolls is finished on CNC machines resulting in high surface accuracy and bright shiny finish of the rolls. DeeTee has a production capacity to make rolls up to 900mm in diameter.
TPI: Brief us about your market footprint, exports, and major clientele.
AB: We cater to clients nationwide and globally and our clients are from diversified industries. Being the first in this line in India to be certified with ISO certification, DeeTee caters to about 50 percent of the requirement of such tools in the domestic market – the “largest in India”. All steel giants in the domestic market are our customers like AMNS, JSW, Jindal, Apl Apollo, TATA Steel, etc. This is evident from the fact that DeeTee is exporting 50 percent of its manufacture to more than 65 countries like USA, Canada, UK, France, Australia, Germany, Korea, South Africa, Malaysia, the Gulf Countries, Southeast Asian countries, etc across the world. We have been awarded a Certificate of Export Excellence by the Indian Government.
Also Read: GL Control GmbH: Laser Measurement of Tubes and Extruder Bore Holes
TPI: What is your USP that keeps you abreast of your competitors?
AB: DeeTee stands for – Determination to Establish Excellence Through Efficiency & Expertise. Maximum durability and reliability are the hallmark of every DeeTee product because of this it has won a place in the topmost ranks of the global steel and metal industry. This competitive advantage enabled DeeTee to create superior value for its customers and superior profits for itself. An experience of almost five decades has given DeeTee a competitive edge over competitors with far-fetched market repute.
TPI: Can you share some of the recent developments undertaken by your company and their significance?
AB: As part of our expansion plans, we will be coming up with a new facility with a total plant area of 1,50,000 square feet, along with an advanced heat treatment facility and as well as other new imported machinery. This will definitely increase our monthly production capacity to a large extent as well as allow us to manufacture larger diameters and longer parts.
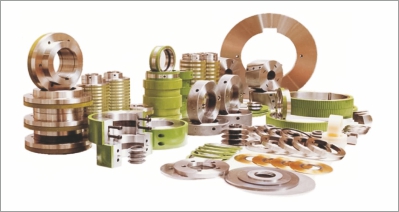
TPI: With a rich experience of 45 years, how have you maintained the quality of your products?
AB: We have in-house state of art heat treatment facilities that give excellent control over product quality. Our facilities include salt baths, induction hardening, cryogenic and sub-zero treatments, etc. We have skilled manpower and are regularly updated on technology. We also have a well-managed H.R. We have an economical and trusted vendor setup. Our state-of-the-art infrastructure is a versatile and well-equipped plant for flexibility in the product. Our offices/ agents are spread over India and important foreign markets for adequate representation and ease of transactions. We have a never-ending dedication to quality, excellence, and reliability, earning the trust of domestic as well as international clientele. We do not compromise on the quality of raw material procurement and consumption leading to high-quality finished goods.
TPI: What are your thoughts on the future of the tube and pipe industry vis a vis your vision and plans for your company’s future?
AB: We feel that looking at the present market scenario, the future of the tube and pipe industry is very bright in India because of the “Make In India” policy which is strongly promoted by the Indian Government. Our vision as DeeTee Group is to become the largest manufacturer of forming and cutting tools in the world.