Founded by Christian Haeusler, the Switzerland-based mechanical engineering company began as a small locksmith shop and has since expanded its presence to around 70 countries, becoming a leading plate bending technology provider. The company began exporting in 1952 and made its first overseas delivery to India in 1955. Today, HAEUSLER is renowned for pioneering the world’s first autonomous bending process. In an exclusive interview with Tube & Pipe India, Mr. Klaus Höferlin, Director of Sales and Projects, HAEUSLER, shares about the company’s latest innovation and the evolution of the tube and pipe industry.
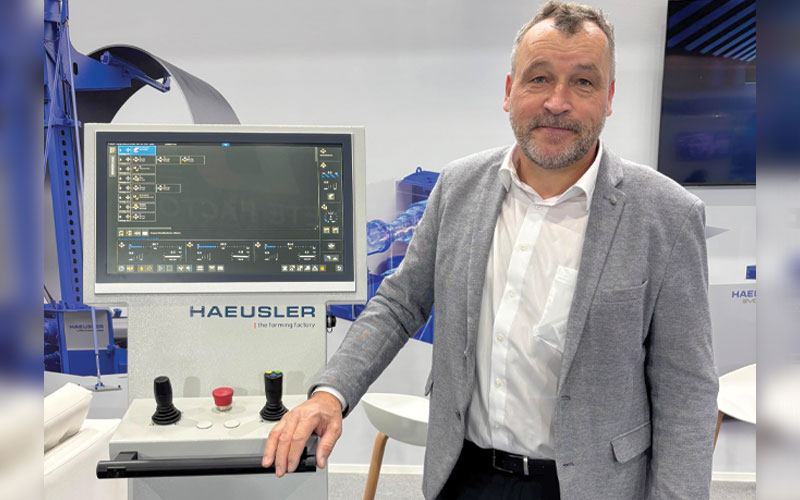
Tube & Pipe India: Can you please give an overview of the company?
Klaus Höferlin: Established in 1936, the HAEUSLER is a privately owned, technology-driven company, specializing in the production of bending machines. Our core product category is plate bending machines, which account for approximately 50% of our business, with the remaining 50% derived from special machines.
TPI: Can you tell us about your manufacturing setup and production capacity?
KH: Our company operates two workshops, located in Germany and Switzerland, where all our products are manufactured. We have in production a strict split in serial and customized products, whereby in design and sales we combine these two fields, in order to maintain cutting-edge technology supported by our strong engineering force. Serial products are produced in highest efficiency and customized machines are crafted individually.
We manufacture approximately 35 to 40 machines annually, with a yearly turnover of approx. EUR 50 million, depending on the scale and scope of our projects.
TPI: What sets your machines apart from the rest of the competitors in terms of innovation and upgradation?
KH: The USP of our machines is that we are at the forefront of technology. While we may not weld, mill, or paint better than others, we consistently lead the industry in innovation. For example, in 1974, we were the first company to build plate bending machines with hydraulic drives, which have since become state-of-the-art machinery.
In 2019, we pioneered the development of machines with electric drives, and once again, we are leading in this field. Our control system sets the benchmark, establishing the standard that others follow. Additionally, we continually innovate, developing new systems each year to integrate into our machines.
This is possible because we specialize in tailor-made machines and have extensive engineering capacity. The valuable innovations we develop for special machines are seamlessly incorporated into our standard serial machines. By consistently leading in technology, we remain competitive on a global scale, which is no small feat.
TPI: Can you share with us your product lines?
KH: As mentioned, 50% of our product portfolio consists of plate bending machines, with two primary types: 3-roll plate bending machines and 4-roll plate bending machines. The 3-roll plate bending machines accommodate output of up to 30 pipes per hour for pipe mills, plate widths up to 24 meters for shipyards and plate thicknesses exceeding 250 mm for nuclear industry. These machines are designed for heavy-duty applications. On the other hand, our 4-roll plate bending machines are known for their precision, advanced automation, and ease of operation, providing maximum efficiency with minimal complexity. These plate bending machines serve industries such as aircraft manufacturing, shipbuilding, on-offshore, wind industry and for pipe producers.
In addition to plate bending machines, our company offers a variety of other equipment, including LSAW pipe production lines, tube coiling machines, installation equipment, and specialized forming machines.
From the development of single roll forming machines for pipe mills, we have evolved into an integrator of complete production plants. In the oil and gas sector, we collaborate with partner companies to deliver comprehensive production plants. However, we retain our expertise and engineering in plant layout and process engineering, ensuring the highest standards in all our projects.
TPI: How do you stay ahead of the curve in terms of product development innovation? Are there any new developments happening in the company?
KH: We handle everything in-house—mechanics, hydraulics, controls, and HMI’s. Last October, we introduced a new series of 4-roll plate bending machines, our VRM NEO. We’ve combined the best elements from the latest state of the art control system and full electrical drive technologies with the proven durability and reliability of Haeusler rigging machines. The result is a reliable, energy-saving and easy to handle bending solution.
This year, a type of 3-roll bending machine is following which will change the game of using a 3 roll bender completely.
In the pipe mill industry, beside the leading edge roll forming development, we have our tack-welder and full-body pipe expander as the leading machines in the market. We’ve reached the point where we are preventing any rotating actions during stacking or where we can incorporate online banana measurement within expanding.
Also Read: Warpp Engineers to Produce 6,500 Welding and Cutting Machines
TPI: How do you envision the evolution of the tube and pipe industry?
KH: Since we have designed and produced many LSAW pipe mills worldwide, we believe there is actually a slight overcapacity in the sector, with many companies facing a lack of demand. As a result, we don’t anticipate a significant number of new greenfield projects. However, with our specialized machines for forming, welding and cold expansion, we are ready for active involvemet, whenever there is a modernization opportunity.
In the future, our focus will continue on selling individual machines for pipe forming, welding, and expansion. This will remain a key part of our business moving forward.
TPI: What are your goals and plans for the future?
KH: Our goal is to maintain our current size. We are not focused on rapid growth but prefer to stay as a company with around 120 employees. Our main target is to preserve the spirit of innovation within the company to maintain our solution provider image. To satisfy our clients by providing smart solutions is essential for staying viable in countries like Germany or Switzerland, where production costs are high. Being close to our clients, and being highly innovative and productive is the key to sustaining our success in such environments.