INfab, an O’Neal Inc. subsidiary, acknowledges the significant role that Technar’s Rotoweld 3.0 automatic rotary pipe welding cell has played in its emergence as a self-dependent company. The twin-bay welding cell undertakes the work equivalent to 4-5 manual welders.
May 23, 2023
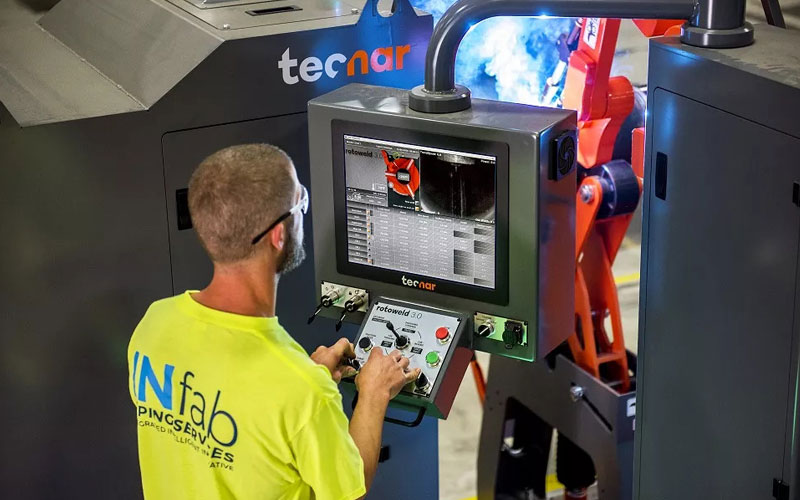
Technar’s Rotoweld 3.0 automatic rotary pipe welding cell is a twin-bay cell used to weld carbon steel pipes from 3”-42” OD and stainless steel from 6”-42” OD for customers in the chemical, wastewater, and pulp and paper sectors. When welding the complex spools of large-diameter pipe, the automatic cell routinely does the work of four or five welders. INfab, an O’Neal Inc. subsidiary, was launched in 2019 and equipped with a Rotoweld 3.0 among other equipment.
At INfab, two different welding guns are used with the robot to enable 100 percent CO2 surface tension transfer to perform the initial root pass on its pipe welds and spray arc transfer welding to fill the rest of the gap. Rotoweld’s 4D Synergy welding technology simultaneously tracks and adjusts four welding parameters: traveling speed, wire speed, oscillation, and arc power. The unit uses a feature called Rotomatic to automatically maintain the position of the arc in the bevel and accommodate 100 percent of gap variation from 2 to 4 mm in open welds, even when traveling at full speed.
When the cell encounters tacks in the weld path, it can compensate to make sure that the welding arc is always in front of the weld puddle.
Mr. Jason Jones, Vice President of INfab, explained, “You have to do a fair amount of work upfront in breaking the spools so that you’ve got enough room to roll. Our superintendent and our plant manager will make sure that the spool is built in what we call ‘subs.’ They’ll literally mark on the spool sheet that this is going to fitter A, B, or C, and this is the order that it’s going to go to the Rotoweld so that when it comes back, those individual pieces, those individual subs, can get final fit and final weld.”
He further stated “You have to build it in an order that allows you to put the most welds on the Rotoweld. If you don’t spend that time, you may only get one [weld] where you could have gotten four or five welds on a given complex spool. So, when you account for that, then you account for the time it takes to load the positioner with these spools. Our data shows we are getting four to five times the throughput that we do with a manual welder.”
According to Mr. Alexandre Nadeau, President & CEO of Tecnar, a shop that has done the proper setup should be able to put 70% of the welds on a given spool across a Rotoweld, more is also possible. He comments, “If you’re below that, you’re probably not thinking through your sequencing properly.”
Also Read: BLM GROUP Launches VGPNext CAD/CAM Programming Software for Tube Bending Machines
INfab has tailored its operation around the technology from the beginning. This saved the company the pain of switching from manually intensive processes to more automated ones and kept it ahead of the curve in dealing with the shortage of skilled welders. It has since been significant in raising the annual revenue to an average of USD 20 million. The company which started working mainly with existing O’Neal customers, now does 70 percent of its business with companies that it solicited on its own.
Mr. Jones stated, “We’re not a union shop; we’re an open shop. There’s no question that the craft labor market, especially for qualified pipe welders and fitters, is shrinking, and when you have a machine that can do the work of four to five manual welders, in our case, you’ve got to leverage that.”
The automated cell enables INfab to make the most of its 50,000 sq. ft. of floor space, as Mr. Jones explained, “We’re not a massive facility by any stretch. You can only fit so many manual welders in a given square foot [area]. Especially when you’re dealing with a large pipe, you can get really clogged up really quickly. Your flow is incredibly important. [The welding cell] has allowed us to maximize our revenue within our footprint.”