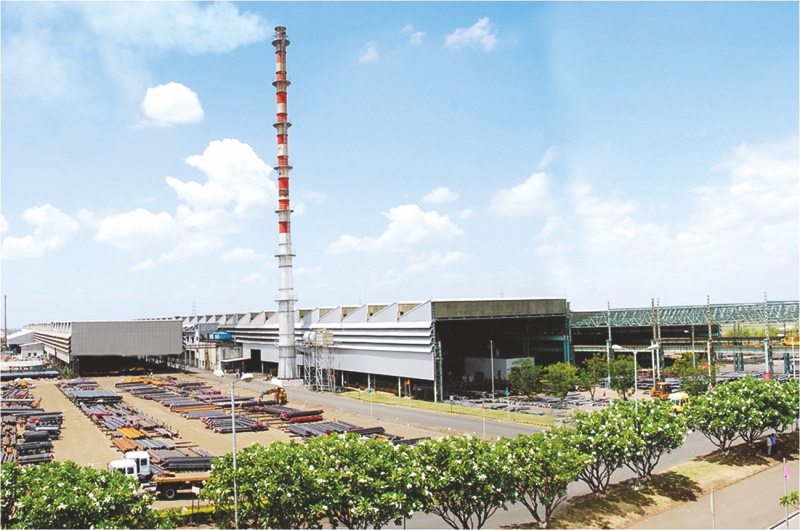
Started in 1977, with a unique combination of assel mills, a premium quality finishing(PQF) mill, and an integrated steel manufacturing facility, Indian Seamless Metal Tubes (ISMT) is one of the most diversified manufacturers of specialized seamless tubes. ISMT produces both hot-finished as well as cold-finished seamless tubes catering to applications such as the manufacture of auto-components, bearing races, OCTG products, drill rods, boilers, heat-exchangers, etc. Tube & Pipe India feels fortunate to converse with Mr. Nishikant Ektare, Managing Director, ISMT as he elaborates on the business plans to aggressively push and maximize capacity utilization of the steel and tube plant and invest CAPEX for various debottlenecking operations.
Tube & Pipe India: Please tell us about Indian Seamless Metal Tubes (ISMT) Limited, highlighting the company’s business journey, major milestones and achievements.
Nishikant Ektare: ISMT was started by a group of technocrats for production of bearing tubes through seamless route as an import substitute in 1977 and the first plant at Ahmednagar commenced operation in 1980 with 1 assel mill and an installed capacity of 15,000 MTPA. Later the company expanded by setting up another mill of similar capacity as the demand for tubes was continuously rising. The company as part of its strategy to be self-reliant for the raw material- steel billets, decided to set up a steel plant and become a fully integrated manufacturer in 1993 when the GoI liberalized the economy. The steel plant then christened ISSAL (Indian Seamless Steels & Alloys Ltd) was commissioned with an installed capacity of 3.0 Lakh MTPA commenced commercial production in 1995. Subsequently, the company also acquired KSTL (Kalyani Seamless Tubes Ltd.) from the Kalyani group in 2000 thus marking the foray into larger diameter tubes for varied application. In the year 2005, all the 3 companies were merged and the new entity ISMT Ltd was formed. ISMT Ltd., also acquired Structo Hydraulics AB in Sweden to cater to the hydraulic segment in Europe and was a leading supplier to the large OEMs.
The company went through severe financial crises with Chinese dumping and the market slow down post 2012 and was reeling under losses and strained operations. In March 2022, Kirloskar Ferrous acquired a majority stake in ISMT Ltd and with this the new management came on board. The management went about addressing the major concerns facing the company viz restoring positive net worth, negotiated sourcing of RM, improving customer satisfaction, aggressive market push for volumes to load the plants for full capacity utilization and also focusing on costs with a view to improve contribution. The result of these actions helped the company to turnaround in the very 1st quarter after takeover.
“In March 2022, Kirloskar Ferrous acquired a majority stake in ISMT Ltd and with this the new management came on board.”
TPI: Kindly give a brief walkthrough of the manufacturing facilities, infrastructure and machinery setup along with the production capacity.
NE: Steel Plant at Jejuri: The company has installed a EAF (electric arc furnace) with 55 MT capacity capable of making 18 to 20 heats per day with downstream facilities of LRF( ladle refining furnace), VD/VOD (vacuum degassing), concast, rolling mill, heat treatment furnaces and supporting infrastructure like the fume extraction, oxygen plant, laboratory etc to effectively produce 3.0 Lakh MT of billets and about 1.50 lakh MT of rolled bars. About 70% of the production is for captive consumption and the balance is sold to the market for bearing and auto application. We cast billets in dia 180, 200 and 225 mm and rolled bars from 25 mm to 90 mm with varied alloy compositions. We also make super critical T9 and T91 grades for the boiler application.
Tube Plant at Nagar: The Company has an annual installed capacity of 60,000 MT for tube rolling and around 55,000 MT for finished tubes. The plant has 2 assel mills with the associated heating furnaces, finishing lines, non-destructive testing and allied facilities. The Nagar plant caters to smaller dia tubes in the size range of 16 mm to 140 mm and has the cold draw, cold pilger and the hot finish tube manufacturing facilities. The plant is equipped with all the finishing and testing equipments including heat treatment and handling infrastructure. The Nagar plant also has 2 sub divisions wherein smaller dia tubes and components are manufactured. The major segments serviced by the Nagar plant is automotive, bearing and mining industry.
Tube Plant at Baramati: The company has an installed capacity of 3.0 Lakh MT of rolling and around 1.50 lakh MT for finished tubes. The plant has 1 assel mill capable of producing tubes from 7” to 10” and a PQF mill capable of producing from 1.5” to 5.5”. The associated infrastructure of handling, heat treatment, testing facilities are available for each of the types of tubes being manufactured whether they are cold drawn, casing, tubing or hot finish. The Baramati plant caters to a wider range of markets and serves oil & gas, power, refineries, auto, hydraulics, mining and industrial segments.
TPI: Please elaborate on the product range of ISMT Limited, emphasizing on their features, applications and advantages.
NE: Steel:
Features: Rolled bars from 25 mm dia to 90 mm dia also spheroidized and annealed as required
Application: Varied- bearing races, automotive shafts, spindles, gears, rollers etc.
Advantages: EAF route clean steel, low Ti grades for unique bearing applications, short delivery cycles, small batch quantity and ready availability
Tube:
Features: Size range from 16mm dia to 273 mm dia, quenched and tempers, normalised, cold drawn hot finish, cold pilgered etc.
Application: Across diverse segments of automotive, bearing, boilers, projects, oil & gas, general engineering, hydraulics, mining etc.
Advantages: Best in class quality, superior surface finish, traceability, high alloy tubes, moderate MOQ
TPI: What kind of capacity expansions has ISMT recently undertaken and is planning in the near future? Please elaborate on the new infrastructure, machinery setup, and manufacturing and production capacity of the recent expansion.
NE: We are planning CAPEX to de-bottleneck the finishing capacities at Nagar and BMT to be able to realize the full capacity of the plant. Our endeavor is also to restore all equipment to the original working conditions after years of neglect and wear. With the planned CAPEX over 2 years we intend to take the saleable capacity to 2.5 lakh MT of seamless tubes. The major investment will be made in shed extensions, FG storage, NDT equipment, material handling, roads, drainages and compound wall.
TPI: Could you elaborate on the company’s vast clientele and market share?
NE: The company operates in the major segments of automotive, bearing, general engineering, hydraulics, mining, export, projects, defense, boiler, oil & gas, re-drawers and trade and is Tier 1 or Tier 2 supplier to the OEMs. ISMT boasts of predominant market share in the Auto and Bearing segments and is pursuing improving market share in the Oil and Gas sectors as the market is booming and there exists huge opportunities.
Our products find application and are supplied to the leading in the passenger &, commercial vehicle, tractor, agricultural implements, construction equipment, hydraulics, mining, defense and oil majors like ONGC, Oil India, major project companies like L&T, ThyssenKrupp and power plant equipment suppliers like Thermax, ISGEC etc.
Presently, ISMT has a market share of approximately 17% in the seamless tube business and we have lined up plans to improve our market share to >25% in the next 5 years.
Also Read: Vishal Pipes Envision Escalationof 75% in Overall Production Capacity
TPI: What according to you are the major USPs contributing to ISMT Limited’s growth in the industry?
NE: Our major USP is the integrated steel manufacturing facility that gives us scope for development of new grades, shorter lead times for supply and also takes part in niche small volume business. We also can work closely and quickly for adoption of process changes and emergent requirements of our esteemed customers.
TPI: As major players in the tubes & pipes industry, kindly shed some light on the current scenario, ongoing challenges and upcoming opportunities in the global and Indian tubes & pipes market.
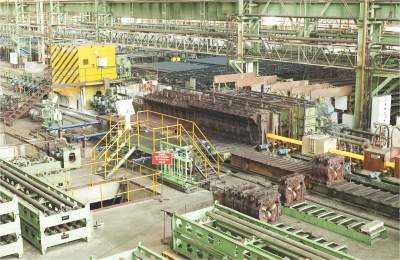
NE: The seamless tube market in India is slated to grow at a CAGR of 7% for the next 7 to 8 years considering that most of the segments are growing whether it is oil & gas, power projects, automotive and defense. There is also huge demand coming in from North America and the Middle-east owing to the strategies of these countries to have an alternative to China. Indian seamless tube manufacturers will have to build capabilities in product development for a wide range of applications like geo-thermal and specialized oil & gas to partake in these business opportunities.
Post opening up of China after COVID 19 by October 2022, we have witnessed huge quantities of seamless tubes and rings coming into India at substantially low prices thus de-stabilizing the business in the short term.
TPI: What are the company’s long term and short term plans for growth in the future?
NE: Our short term goal is to aggressively push and maximize capacity utilization of the steel and tube plant and invest CAPEX for various de-bottlenecking operations. As part of a long term strategy, we would foray into seamless tubes larger than 10” dia and necessary investments will be made in the coming years.