Founded in 2007, NEXTSENSE provides trailblazing profile measurement systems which are based on non-contact laser measurement technology. This enables the users to glean knowledge based on – precise information without distortion, variation, and approximation. There are three major industry segments – Automotive, Railway, and Steel – for which NEXTSENSE provides its Calipri-based solutions. In an interview with Tube & Pipe India magazine, Dr. Ralph Foehr, Global Sales Manager Steel Applications, NEXTSENSE GmbH, talks about the Company, its solutions for the steel industry, innovation in terms of production technologies, recent developments, and the way ahead.
“The tube and pipe makers must shift away from their conventional manufacturing processes and move towards intelligent processes… For this, precise measurement systems are crucial.”
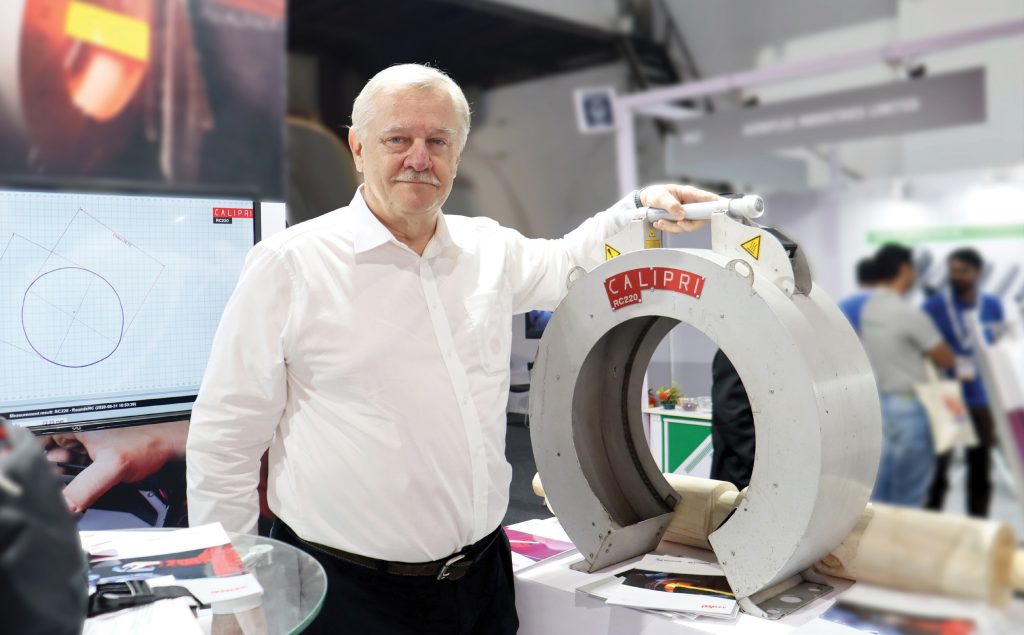
Tube & Pipe India: Could you please give us a brief outline of the business journey of your company along with crucial milestones?
Ralph Foehr: NEXTSENSE GmbH is an Austria-based company. We have a workforce of roughly around 100 people in Austria. The company has been taking care of laser-based measurement systems for seventeen years. For four years, we are a part of the hexagon group, which is a huge name in the machine intelligence and automation systems industry. There’s been a growing inclination to glean more information about the dimensions during the production process. In this respect, the measurement has to be extremely precise. About ten years ago, most of the industry players, which also include some of our clientele, were happy with relatively simplistic measurements, for example, diameter in a horizontal direction and in a vertical direction. This is not enough in today’s times. The manufacturers want to check if certain rolling defects are occurring. It is also important to note if these rolling defects can be detected reliably so as to notify the operating crew for them to take any remediate steps during the production process. Our thorough focus is on integrating a lot of technical directions in the production industry.
TPI: Kindly cast some light on the infrastructure, manufacturing capabilities, and machinery installed at your facility.
RF: Since our capabilities lie in the production of electronics and software, thus, the role of large-scale facilities is not a major requirement for us. In fact, we have partnered with a few reliable suppliers who assist us in mechanical part-related operations. At present, we take part in the assembly of the electronics. Moreover, the CAD is also done with us. It can’t be overstated enough that the most important part of our products is the embedded software in the systems.
Also, laser sensors are an integral part of measurement systems. Since the raw signal is usually not proper, one has to do a lot of filtering and calculation so that one gets the right and precise data from the system.
TPI: What all products are there in your portfolio and what are the key strengths and applications?
RF: We, at NEXTSENSE, are producing laser gauges for three different industries. Firstly, in the ‘automotive’ industry, we enable the production process to find out whether or not the production worked well with our range of technological solutions. For the ‘railway’ industry, we provide solutions for profile measurement for predictive maintenance where we assess the working of wheels, brakes, rails or switches – we have the right solution for any measurement task. Finally, in the ‘steel’ industry, which has been the industry with which we started our journey, Nextsense offers solutions to identify surface defects and profile deviations, particularly on long products. Thus, we are enabling steel rolling mills in this aspect, for instance, in product segments like wire rods and tubes; we assist the producers in defining the cross-section of that product during production.
I would like to emphasize on the solutions for the ‘Steel Industry’. In principle, we have two big groups of products – mobile gauges which can be carried to the position which is to be measured and stationery gauges which are immobile. These devices allow you to get information about the diameter and other characteristics. We started the supply of stationary gauges 17 years ago and we started in the rail rolling industry. For four years or so, we have diversified our business and we have started serving other industry segments such as the wire rod mills, bar mills, and pipe mills.
TPI: Data Analysis and Artificial Intelligence are the future of new manufacturing systems. Please share your opinion on the same.
RF: Realistically speaking, only those mills, who know how to use the data in a proper manner, can create the right SOPs, to be referred to in the production process which is quite advantageous for the manufacturers.
Meanwhile, the people associated with the financial department of the mills or those taking care of the financials, are majorly concerned with the Return on Investment (RoI). In this regard, I would say that the measurement process itself doesn’t save money in a direct way. It is only what you do with the data, which you then integrate into the production operations. This enables in saving the capital. This enables us in making measurement-related decisions in a much faster way with our different measurement systems which also gives the required feedback to the operations team.
Further, there is another driving factor which we are foreseeing, and which is pushing us now in a certain direction. In the next 20 years, steelmaking will change completely with the prevalence of green steel. For green steel production, the processes will be different keeping in mind the unique mechanical properties of green steel. Now if one uses hydrogen in the blast furnace instead of coke, then there is no carbon in the iron. It means that one will need to find a different way to inject the carbon into the iron. In the beginning, that material will have different mechanical properties. This also means that we will need to ensure a steeper learning curve to get used to the new mechanical properties. The rolling mills see this material first and there we need to watch the process more thoroughly. The said learning curve can only be achieved if the industry players pay attention towards collecting more knowledge and understanding of the processes, using Big Data analytics and Artificial Intelligence to understand how the new rolling process works.
TPI: Please shed some light on the clientele of your company in the Indian market. Also, kindly share your outlook on the tube & pipe industry.
RF: In the Indian market, we have been supplying our products for the last ten years. We have established a strong repute and our customers include the Steel Authority of India Limited (SAIL), Jindal Steel and Power Limited (JSPL), and so on. These are a few of the major customers we’ve been serving. In the coming future, we would like to increasingly collaborate more with the tube, wire rod, bar, and tube mills.
In terms of our portfolio, we are looking forward to expanding our presence in the tube & pipe industry to fulfill their requirements related to measuring systems. We aspire to get more inquiries for our solutions from the tube & pipe industry. Nonetheless, it will be an initiative that has to be directed by the manufacturers. The tube and pipe makers must shift away from their conventional manufacturing processes and move towards intelligent processes. This is where we come into the picture. The need to become smarter in the production processes has become more urgent than ever before. For this, precise measurement systems are crucial. In our understanding, we are quite enthusiastic to serve the requirements of the tube & pipe industry.
“We would focus on: increasing our dependence on software/machineintelligence- based systems.”
TPI: What is your technology and business roadmap for the future?
RF: Essentially, we would focus on: increasing our dependence on software/machine-intelligencebased systems and growing the usage of standardized components in the hardware. For instance, in a rolling mill, if one can only afford to put just one gauge inside because it’s expensive, we would need to make the gauges less expensive so that many more gauges can be placed inside so that one can follow the complete rolling process. This is the major focus area for us.
Also Read: GMT Industries Limited: Aiming Exponential Growth through World-Class Products and Services
At a later stage, all these data and information are integrated as A.I.-models, i.e., the simulation of so-called digital twins. This will enable to go through all the details much more thoroughly and asses the activities in the facility. Hence, in this respect, we would like to increase our inclination towards software and A.I.
TPI: Is there anything else you would like to add with respect to the Indian market?
RF: The Indian market is quite challenging. It has been around 10 years that we’ve been coming here on a regular basis. In the future, we would like to associate with more such companies who are willing to make their factories smarter. This is a large-scale transformation which would not happen automatically. It will entail the right strategies and tools to drive such changes. In fact, the disposition of the customers in this regard will be significant. Their investment in the right personnel and the right processes would be a determining factor. Presently, the Indian manufacturing industry is booming, which is a positive indicator. It can be said that the situation in the manufacturing industries in China was at a similar level, about 20-30 years ago. Also, the investment of China in quality and supporting technologies was not that considerable. This was because they could still sell without anybody checking on the quality-aspect.
Right now, the demand dynamics in the global market have become more than the industry can deliver. Thus, quality, in principle, has become less of an issue. However, the situation is changing. Today, in China, one will find the most modern and state-of-the-art mills. This has been made possible because of their willingness to invest in improving production technologies. Since there is a degree of competition inside the country, they strategize to position themselves in a completely different way. What I am hoping is that India is paying diligent attention towards the quality-related parameters of the products manufactured.