Parth Equipment Limited, established in 1988 is a leading company specialized in engineering and manufacturing of plants for production of stainless steel and carbon steel tubes. Based in Ahmedabad, Gujarat, the company’s production infrastructure consists of 4 manufacturing plants, more than 70 machine tools, and around 200 employees creating a diverse portfolio of over 75 models in more than 15 product categories. They have vast clientele spread across India as well as abroad including the USA, the Middle East and Africa. They are in process to enhance the manufacturing capability further to produce 100 machines per year by FY25, and aim to develop DFT mill and automatic offline tube cutting machine in near future. In a recent interaction with Tube & Pipe India, Mr. Arth Shah, Executive Director, Parth Equipment Limited, talked about the company’s journey, success story, product portfolio, recent developments and innovations. He also talked about company’s vast clientele, and shared his views on the future of the tube and pipe industry.
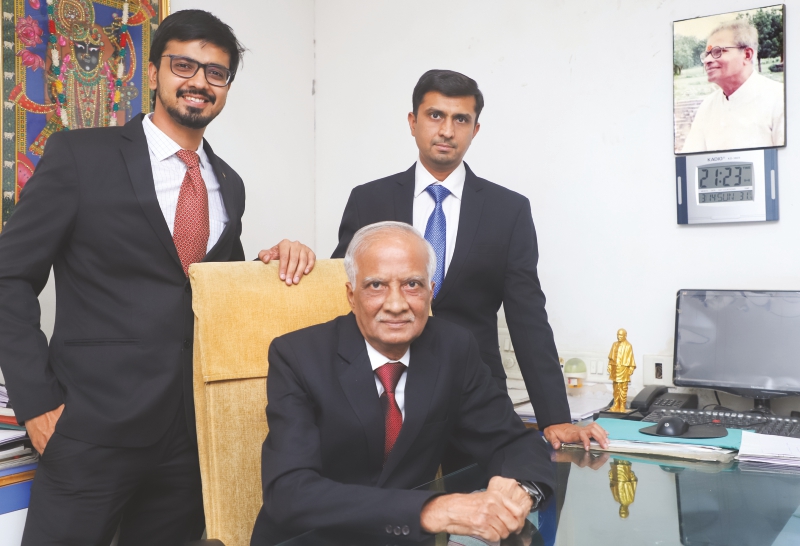
Tube & Pipe India: Parth Equipment Limited looks back on a history of more than 30 years. Please elaborate on your journey, crucial milestones and success story.
Arth Shah: Our journey began in 1988 with a small workshop in Ahmedabad, which was manufacturing components for the tube industries. Under the leadership of Mr. N T Shah, a technocrat with a master’s degree from IIT Bombay, our organization went on to become the market leader in supplying tube mills and plants for the production of ferrous and non-ferrous tubes. We received the opportunity to supply our first tube mill for stainless steel tubes in 1991. Owing to the sturdy design and superior build quality, Parth Equipment continued receiving opportunities to add various machinery and new tube sizes to the product basket over the journey of 35 years. At present, our product portfolio consists of over 75 models in more than 15 product categories. Genuine commitment to the most stringent quality levels, utmost care for specific customer requirements, and excellent after-sales support have been our tools to success.
Over the years, we have increased our production capacity. At present, our production infrastructure consists of 4 manufacturing plants, more than 70 machine tools, and more than 200 employees. We are in process to enhance the manufacturing capability further to produce 100 machines per year by FY25.
TPI: Please share with us your offerings and plant portfolio for the production of tubes and pipes.
AS: We are one of the few manufacturers to supply a complete range of equipment. Our diverse product portfolio consists of machinery required in stainless steel, carbon steel, and non-ferrous steel tube plants. We supply equipment for both the welded and seamless tube industry. This approach helps mitigate risks and enable us to perform well even in challenging situations. We offer tube mills for stainless steel and carbon steel tubes upto 10″ NB, tube straightening machine upto 10″ NB, tube draw bench upto 150 MT pull capacity, round and square pipe polishing machine, and hydro testing machine upto 10″ NB. We also specialize in flying coldsaw cutoff machine, coil slitting line, pilger mill dies and mandrels, tube swaging machine, and tube-end chamfering machine.
TPI: What developments and innovations are you inheriting in your plants and technology for the tubes & pipes industry?
AS: We focus on value addition through high-end engineering. We are a group run by IITians and technology enthusiasts. With a strong backbone of industrial setup and a quality-conscious mindset, we thrive to succeed in the new atmosphere, set out with a single goal to do something new and better which is done by investing in research and development. We are continuously adding new automation features to our machines to increase productivity and reduce manpower. We have made improvements to make our machines compatible with Industry 4.0. In the future, we want to develop the direct forming technology (DFT) mill to produce square and rectangular tubes directly without tool change. We are also in the process of developing the automatic offline tube cutting machine required especially in the automotive industries.
TPI: Brief us about your manufacturing locations and manufacturing capacities for technologies related to the tubes & pipes industry.
AS: Parth Equipment Limited is located in Ahmedabad, Gujarat, the growth engine of India. Our headquarters, machine shops, roll manufacturing facility, fabrication shop, and assembly workshops are situated over an area of 1,00,000+ square feet in the industrial epicenter of the city, making it the largest facility in India among this industry. We have a brilliant workforce comprising of engineers, technologists, machine operators, quality inspectors, sales and marketing professionals, and others. Our machine shops consist of CNC turning centres, vertical machining centres, CNC plasma cutting machine, heat treatment furnace, surface grinding machines, bore grinding machines, CNC cylindrical grinding machine and many more conventional machine tools, making it one of the most advanced machine shop. We are using state-of-the-art CAD-CAM software to program the CNC machines to produce complex geometry. We have installed solar power plants at our factory to reduce carbon footprint and promote sustainable development. The production planning and inventory management of our 25,000+ SKUs is controlled by the ERP software.
Also Read: OM TechCorp: Consulting Services for Industrial Seamless Stainless Steel Tube Production
TPI: Parth Equipment Limited stands out for rigorous process control. What additional services and solutions do you provide to your clients apart from the capital-intensive plant and infrastructure.
AS: Apart from supplying machinery, we offer services related to installation and commissioning of the equipment supplied by other OEMs. We give technical guidance related to the processes and equipment requirements to our customers for turnkey projects. We have a vast experience of cold roll-forming technology. We have designed and manufactured the tooling required for the production of various unique profiles and open-sections, which has given a competitive edge to our customers. We also supply customized electrical panels and hydraulic powerpacks for the tube industry.
TPI: Tell us about your vast clientele in India and globally catering to the tubes & pipes sector.
AS: We have supplied over 1000 production plants to our valued customers across India as well as abroad including the USA, Middle East, and Africa. Many of our customers have started their industrial journey with our machines, kept on expanding by giving repeat orders, and are now one of the prominent tube manufacturers worldwide.
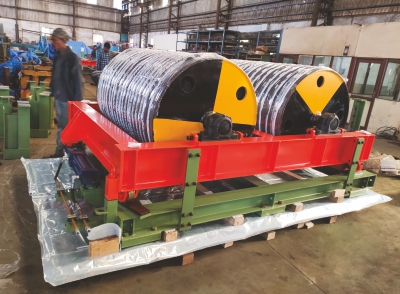
Our well-diversified product basket helped us with a good market penetration across the tube industry. We have supplied machines for stainless steel tube manufacturing in Ratnamani Metals and Tubes, Venus Pipes and Tubes, Jindal SAW, Maxim Tubes, Inoxium Tubi, etc. We have also supplied high-frequency stainless steel tube mills in Ravi Seamless, Arnay Tubes, ASB Tubes etc. Our customers in carbon steel tubes include BHEL, Goodluck Industries, Tata Steel, Rashmi Group, Meta Engitech, Lalbaba Seamless, and many more. We have also supplied plants for copper, brass, and aluminium tubes to various customers like Mehta Tubes, Indian Copper, Multi Metal, Siddhi Group, etc. We have also supplied customized assemblies for the colour-coating and galvanizing lines to our customer Tenova Group, which were exported to Europe and South-East Asia.
TPI: How do you foresee the future of the tubes & pipes industry? What according to you are the factors which are expected to fuel the growth of this sector?
AS: The market for the tube and pipe industry has seen a sharp recovery post Covid-19 pandemic and it will continue to grow over the next decade. The rising export of India-made tubes in the European and American markets and declining imports from China will increase the requirement for “Made In India” tubes and pipes. Government policies and programs, such as the Jal Jeevan Mission and infrastructure projects like railways, metros, expressway corridors, and smart city mission will fuel the growth of the sector.