The newly ordered Electric Arc Furnace Ultimate is designed to produce 1.9 million tonne per annum (TPA) of steel. The order is an important step in Salzgitter’s investment toward the long-term aim of green steel production.
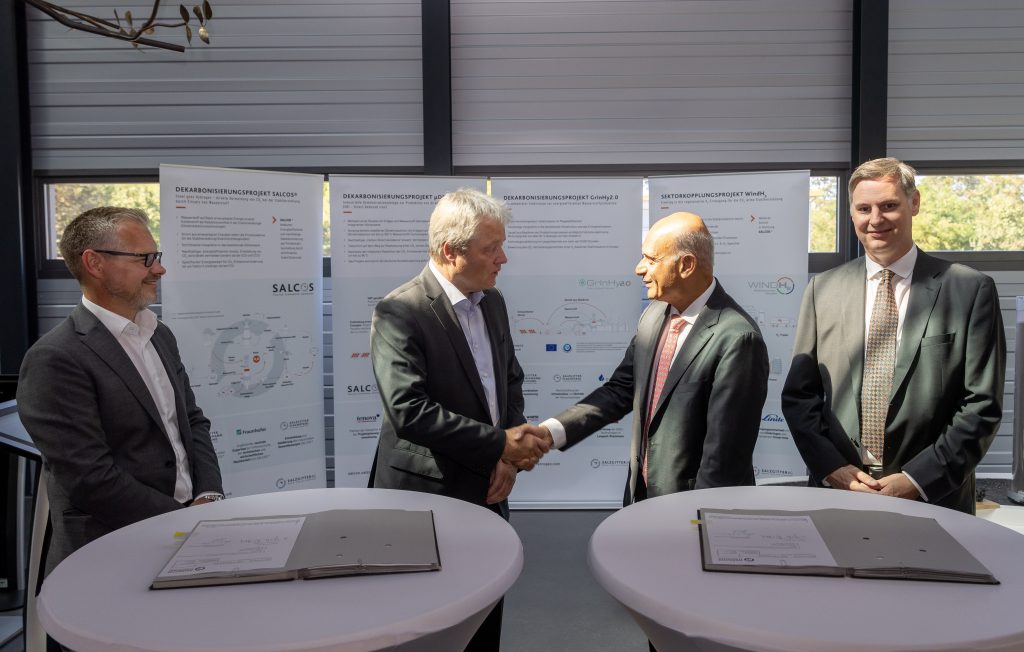
Germany-based steel producer Salzgitter AG has signed an agreement with the UK-based Primetals Technologies Ltd for an Electric Arc Furnace (EAF) Ultimate. With a tapping weight of 220 tonne, the furnace will have a production capacity of 1.9 million tonne per annum (TPA) of steel. It will be implemented at the steel plant in Salzgitter, Germany. The startup is scheduled for the end of 2025.
Salzgitter is investing in the world’s leading and large-scale transformation program in the steel sector. Within the Salzgitter Low CO 2 Steelmaking (SALCOS) project, the producer aims to convert the existing integrated steel plant to green steel production in three stages by 2033. As part of the transformation, two direct reduction plants and three electric furnaces will be built, which will then successively replace the existing blast furnaces and converters. This order for one EAF with Primetals Technologies marks the first step in this process.
“It underscores our ambition to remain a leader in the decarbonization of the steel industry and to set up the Salzgitter site for the future on a lasting basis. With Primetals Technologies, we have a strong partner on our side – true to our strategy of moving toward a sustainable industry,” said Mr. Ulrich Grethe, Head of Steel Production, Salzgitter.
There are numerous reasons which motivated Salzgitter to select Primetals Technologies as the supplier. A sound reference base with several recent successful EAF projects, low consumption figures of the technologies involved, and competence in project management were three main factors. The scope of the order includes engineering, supply, and construction.
“Primetals Technologies is pleased to support Salzgitter AG’s decarbonization projects with the installation of a highly efficient EAF. With our Green Steel technology, we enable low CO2 steel production,” said Mr. Aashish Gupta, Executive Vice President and Head of Upstream, Primetals Technologies.
EAF Ultimate is a part of Primetals Technologies’ new generation of electric steelmaking equipment. It is characterised by short tap-to-tap times, fully automated operation, and advanced control systems. The Salzgitter EAF features dust removal systems, a heat recovery system, a water management system, electrical compensation for grid stabilization, and material handling for alloying materials and additives. It will also include Level 1 and 2 automation and the LiquiRob robot system.
Also Read: Tata Steel Chooses Energiron DRI Technology to take a Major Step into Green Steel Production
The SALCOS project will replace a coking-coal-based steelmaking process with a new hydrogen-based route. This is expected to save around 95 percent of the annual CO 2 emissions of around 8 million tonne. One of Germany’s leading steel and technology groups, Salzgitter has an annual capacity of 7 million tons of crude steel. The group employs 25,000 people worldwide in 150 national and international subsidiaries and associated companies.