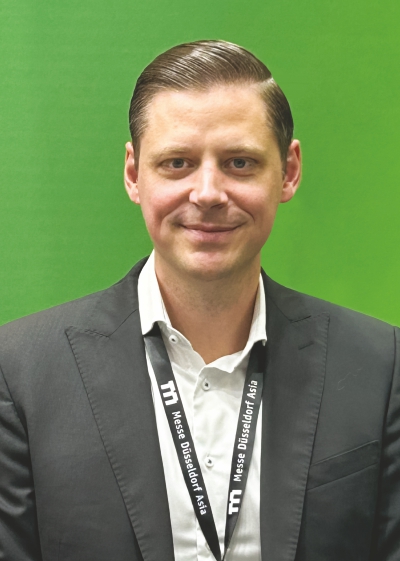
SMS group is a leading technology provider to meet the customer’s needs of today and tomorrow. SMS group’s new lifecycle services portfolio aligns toward making processes more sustainable and energy-efficient. To this end, SMS has combined the areas of electrics & automation, technical service, and digitalization into powerful integrated solution offerings for the customer to maximize the deliverables. This new set-up makes it possible to provide integrated solutions that ensure and even enhance the performance of production plants during their entire lifecycle. The solutions focus on performance indicators, such as plant readiness, product quality, output capacity, and delivery timelines, in addition to, sustainability and safety. SMS group is a full liner for the technology solution in the metal industry and so is in a position to provide a one-stop solution for customers for all their needs.
SMS group has been synonymous with the term ‘Innovation’ in the World of Metals. It has a rich history of ‘150 Years of Shaping the Future’. From a small forging company and supplier to a local industry, it has developed into a global technology company that has had a significant impact on the development of the metal industry. Crucial to this success story was the early orientation towards global markets, the focus on technology, and the adherence to the values of a family-owned company. As a part of its regional strategy, the SMS group is increasing the capacity of existing workshops and also building a new workshop in India. In a recent interaction with Tube & Pipe India, Mr. Bernhard Steenken, CSO, Region APAC & MEA, SMS group, talked about the company, milestones, and developments. He also shared his views on the future of the steel industry in the region.
Tube & Pipe India: Please tell us about SMS group’s plan for the new workshop in India to promote ‘Make in India for the World’.
Bernhard Steenken: SMS group already has a workshop at Khurda in Odisha, east of India with modern and sophisticated manufacturing capabilities along with facilities for providing services. This workshop already serves the challenging requirements of the customers globally. Considering our strong organization set up in India, the success of our Bhubaneswar workshop operations, growing global and regional business, and commitment towards the success of our customers, we are putting up a new manufacturing plant in the state of Gujarat under ‘Make in India’ and ‘Make in Gujarat’ initiatives.
We will be transferring the manufacturing technology from Germany to India along with the development of the latest state-of-the-art manufacturing infrastructure for the manufacturing of technology-sensitive critical equipment for flat products, long products, and forging plants for the global market. This new plant will cater to customized repair, refurbishment, and service solutions including spares to our customers located in western India. This plant will be the perfect blend of German technology, Indian talent, and industry-friendly state ‘Vibrant Gujarat’.
TPI: Tell us about the history, major milestones, and recent achievements of the company.
BS: We are currently celebrating our 150th anniversary, and we feel immensely proud because to survive 150 years in the market, you always need to reinvent yourself and there is a constant need for new technologies and innovative solutions to maintain a competitive edge. Over the years we have been able to partner with customers to give them an edge in the competitive market with the new age solutions. Our goal is to be lifecycle partners and be part of the success of the customer’s journey. Our mission is to turn metals green and to advance climate-neutral and sustainable metals production.
Customers of the SMS group are in various locations – geographically and economically different from each other. Hence, even if the final goal is the same i.e. sustainability and the lowest possible carbon footprint, the solutions would be entirely different. Since within the SMS group, product development is done considering geo-economic factors, it becomes very easy for the SMS group to understand the needs of its customers and accordingly propose the appropriate solution for implementation. Today, the whole world is talking about de-carbonization and it is needless to highlight the pioneering efforts of the SMS group. We have developed solutions for decarbonizing the steel industry, limited not only to existing facilities but also to greenfield installations.
We have the concept to reduce the carbon footprint of existing blast furnaces by up to 60 percent partially through synthetic gas and green hydrogen reduction. Then we have of course these breakthrough technologies where we are reducing iron ore with hydrogen.
A few notable examples are:
- In Sweden, we are building the first full-green steel plant in the world. It is the first 100% hydrogen-based steel plant with CO2 emission reduction up to 95 percent. We do supply from the melt shop to finishing lines. So it’s not only that the upstream is zero emission, but also downstream. Additionally, we use carbon only for the metallurgical processes.
- In Germany, the first hydrogen-based direct reduction plant coupled with open bath furnaces to process BF-grade iron ore pellets would bring a saving of 3.5 million metric tons of CO2.
- In the USA, we have built the world’s Learning Steel Plant
- In India, building the largest BOF melt shop
- In India, the world’s longest rail mill
- In Korea and Thailand, we are building very efficient DC Aura EAFs for substantial reduction of electrical power consumption.
TPI: What is your USP? What keeps you ahead of your competition?
BS: SMS group utilizes its wide range of technologies to shape metal-making processes around the world. Alongside the classic, ore-based integrated solutions, the focus today is on recycling techniques for scrap, metal-bearing residual materials, and minerals. In addition, SMS develops processes for producing alternative fuels and reducing agents that are indispensable for the climate-neutral metal production of the future. Specific to downstream facilities there are a lot of solutions that bring much higher efficiency to our existing technologies that are not so energy intensive.
One of our USPs is our leadership in the efficiency of reheating furnaces and heat treatment furnaces. Best in industry energy efficiency and burners with the capability to use multiple fuels including hydrogen and the SMS’s zero flame technology ensuring reduced NOx levels are key drivers. The most advanced mathematical model ‘SMS Prometheus’ drives the control.
Besides higher yield, the higher efficiency of the mills drives the lowest possible impact on carbon.
TPI: Kindly shed some light on your market footprint and clientele.
BS: Our 150 years of existence stands as a testament to our close relationship with our customers. To better serve them, the SMS group opted for a more localized approach. With the goal of enhancing customer service in the region, an internal reorganization has divided us into four regions on a global scale, and our region is referred to as APAC-MEA, encompassing India, the Asia Pacific sans China, the Middle East, and Africa. This means that approximately half of the world is within our reach.
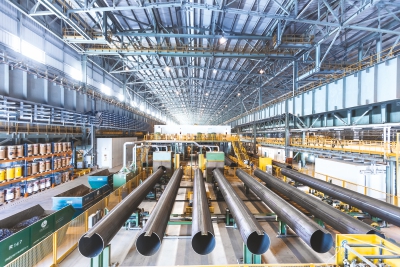
This region is interesting in terms of technology as it spans from Africa to Japan and Korea. It hosts mega mills in India, some of which produce over 10 million tons. We have an entire variety of high-tech, cost-sensitive, and quality-oriented, and we have all these kinds of customers in our region. Our goal is to cater to all of our clients. So we have technologies available for high-quality producers, and we have technologies available for quality niche producers. Additionally, we have technologies and equipment that are suitable for developing countries like Africa which demand lower volumes, high flexibility, and meeting regional market demands. Our strategy is to penetrate the market from all dimensions, in all divisions to ensure we address the varied needs of our customers across the region.
Currently, we are putting a lot of investment here in the region. We are increasing the capacity of our existing workshops and also building a new workshop in India. This is a significant part of our regional strategy and a strong foundation. Actually, our strategy is not just about making things in India; we are taking it a step further – it’s about making products in India for the whole world. Some core components have been relocated to India and we supply out of India to the world, not only our region but to the entire world. This is something we are actively pushing forward. In the metallurgical market, we made our first mark in India around 30-35 years ago and we have become the top supplier in India. India is a vital market for us. If you just look into the installed base in India, there is a lot of SMS equipment. We are immensely proud of this collaboration. Our footprint is not limited to steel but covers aluminium and copper industries too.
TPI: Recently, SMS group announced their internal project SMI 400. Could you shed light on the project?
BS: SMI 400 is in line with our global strategy. We have great confidence in the engineering expertise in India, particularly in automation—a blend of software engineering and traditional engineering processes. As of today, we have approximately 250 people in our workforce only for electrics and automation in India and we want to grow this to 400. Similar to our workshops, these highly skilled and competent resources are involved in driving megaprojects around the world and not limited to the region. The team will strengthen its role covering projects from greenfield to brownfield, including upgrades and replacements for components and drives of existing facilities. We already have the competence for a complete turnkey solution, which will be strengthened with the SMI 400 project. Recently, we secured a significant project to modernize the automation systems for a hot strip mill in India and Indonesia, highlighting the success and expansion of the SMI 400 project.
TPI: What are the outcomes of the MoUs between SAIL, JSW, Tata, and other big companies? How will these MoUs help SMS group to expand in India?

BS: We maintain a long-standing business association with our esteemed customers, including Tata Steel, JSW, Steel Authority of India Limited (SAIL), a public sector enterprise, and other industry leaders. In some cases, we have supplied mills to these customers nearly a century ago in India. These customers are driving the steel industry not only in India but also in the global landscape. So, joining the hands of technology leaders like SMS group and these customers is a symbol of partnership based on trust and technology, and aimed at achieving decarbonization within the industry. We have a joint responsibility to make our world more sustainable. In our specific region, we witness the effects of global warming first-hand. We experience challenges such as flooding and rising water levels, significantly affecting us in a negative way due to these worldwide occurrences. Therefore, we are taking this joint responsibility seriously and we are working on converting these MOUs to effective agreements on decarbonizing the existing facilities. Steel is being described as ‘hard to abate sectors’ which needs the technology to develop joint strategies to create a more sustainable steel industry and to comply with the 2070 net zero target in India. So, the SMS group remains a preferred technology provider for achieving such ambitious targets. Moreover, the ambitious lighthouse projects with H2GS in Sweden are a perfect example of such leadership.
However, in Europe, there are different pre-conditions as these kind of projects are getting subsidized. In Sweden, they have access to cheap green electrical energy, and the market is currently saturated. This leads to a situation where the market is not expanding; instead, it is experiencing a decline. In India, it is different as steel consumption is set to increase from 100 million tons to 300 million tons. So, we have to comply with this and this cannot be done only by DRI or EAF steel-making facilities. It is economically not feasible and also not easy from a supply chain perspective. Therefore we are collaborating with them on implementing especially upstream and downstream green technologies to optimize the existing carbon footprint. In the meantime, we need to take very precise steps and these technologies will enable SAIL, JSW, and Tata to grow and comply with the climate targets and develop a long-term strategy to become net-zero by 2070.
Also Read: Surya Roshni Limited Works to Optimize Steel Consumption with Business & Infrastructural Growth
TPI: How is SMS group setting new standards for sustainability in the steel industry?
BS: SMS group is driven by its mission of #turningmetalsgreen supporting green steel making and a sustainable steel industry. Some of our lighthouse projects include H2 Green Steel and Thyssenkrupp. We use carbon only for the metallurgical processes, the rest all the equipment is electrified, and all the furnaces are fed by hydrogen.
H2 Green Steel – Boden, Sweden
H2GS will be the world’s first renewable hydrogen-based integrated steel plant utilizing high-grade pellets with DRI direct to EAF. Green steel production is based on green hydrogen and electricity based on renewable sources instead of fossil fuels along with two energy recovery plants that produce steam for electrolyzers and downstream processes. SMS group scope includes supply from the DRI plant to finishing lines. This plant will focus on CO2 neutrality, the whole process chain is almost carbon neutral (reduction of 95% compared to conventional steel making). The route for H2GS is DRP-EAF, as the plant will use iron ore pellets with extremely low gangue content. The facility will have a 2.1 million ton per year capacity hydrogen direct reduction plant to transform iron ore into directly reduced iron.
Thyssenkrupp, Duisburg
This will be one of the world’s largest decarbonization projects worldwide, which will have annual savings of more than 3.5 million (currently producing 20 million metric tons) CO2 per year in the future. This plant will have the capacity to produce 2.5 million metric tons of DRI and is scheduled to be completed by 2026. SMS group will supply a DRI plant that can operate on natural gas and hydrogen (0-100) %, two innovative electric smelters, and associated auxiliary units. It is based upon MIDREX Flex, which provides the flexibility to operate on any mixture of natural gas and hydrogen (up to 100 % H2) thereafter; it could be coupled with OBF for smelting and INBA SGP for granulated slag similar to BF slag.
TPI: What are your thoughts on the recent growth of the electric vehicle market in India?
BS: In the broader electric vehicle (EV) market, we also put a lot of focus on this because many of our products are designed to suit the conventional combustion furnace and the standard automotive industry. We not only have innovations in our conventional equipment but also, for example, inventions in disruptive technology such as battery recycling. For instance, we have a joint venture with NeoMetals in Australia, to provide technology that essentially recycles EV batteries to a large extent. We have the first installation in our workshop at Hilchenbach in Germany. Surprisingly, it started as a small-scale industrial facility but the results were so overwhelming that our test facility showed positive business outcomes. As a result, we have now signed the first contract with Mercedes-Benz for their own recycling facility.
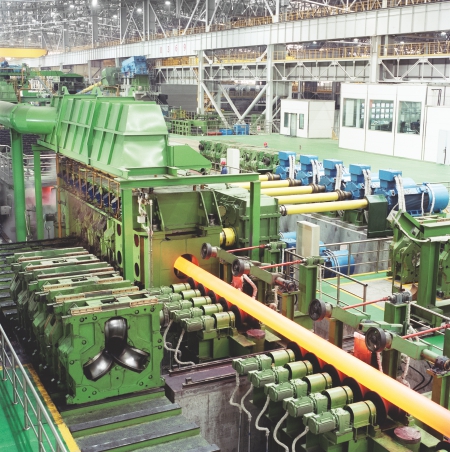
In India, we know that there is a lot of focus on the EV industry, and some of the big industrial players are driving the EV sector. We are in close discussions with them. We have the technologies available to enable them to recycle their batteries for reuse. The EV market also faces challenges. It is not just in India or Europe, but everywhere around the world, we encounter similar problems with the electrical grid. Ultimately, we rely on electrical energy, which is in limited supply. When we look at the environmental impact of the grid, it is not truly carbon neutral. To make the EV market truly sustainable, what we really need is a clean, eco-friendly grid. In my view, that’s the biggest challenge to address for long-term sustainability in the EV industry.
TPI: What are your thoughts on SMS group’s digitalization solutions for the wire and cable/ tube & pipe industry?
BS: In the digital landscape, one of the primary goals is to convert data into information and information into value. This process encompasses the collection, analysis, and interpretation of data to derive valuable insights. These insights, driven by data, enable faster and better decision-making. And it is here that I see the big benefit of digitalization, to collect a lot of information, correlate, and make a proposal that is most likely more precise than human intelligence. Combining domain knowledge with data analytics can be a powerful strategy for optimizing processes and achieving operational excellence in the metallurgical industry. An operating plant has the ability to provide a huge volume of data points. The ability to convert these data points into intelligence is a critical aspect of modern business and technology. It enables customers to remain competitive, adapt to changing circumstances, and deliver data-driven decision-making and digital transformation efforts.
Our strategy focuses on yielding two distinct impacts. Firstly, we have developed tailored applications for specific equipment such as for an Electric Arc Furnace (EAF) and a wire rod mill, and we see very good feedback from our customers on specific process improvement needs. The second pillar of our strategy revolves around ‘end-to-end solutions.’ This aspect gradually becomes more intricate. It involves the accumulation of information from various equipment to optimize production, and energy flows, and enhance planning, scheduling, and sequencing. In the end, these two components align effortlessly because our process-specific applications such as predictive maintenance and predictive processes, enable us to forecast the health condition of machines.
Imagine a situation involving a wire rod mill. By employing our correlational analytics, we can pinpoint when a specific machine is not performing at its best. Rather than promptly commencing a maintenance shutdown, this insight can be incorporated into your planning procedures. Consequently, you can adjust the sequence of production on the line. This adaptation might include a minor change in the product mix, prioritizing grades that are less affected by quality fluctuations due to misaligned rolling blocks. This flexibility enables the uninterrupted production of simpler products, despite the machine’s compromised state. We have invested heavily in digitalization, both in tools and resources. More than 500 people are already working in our digital division, and these 500 people are on top of our 1,500 automation engineers. These two concepts often go hand in hand, as automation can be a part of a broader digitalization strategy to modernize and optimize operations.
TPI: Can you share with us your observations on key market trends in the Indian tubes and pipes/ wires market?
BS: Certainly, when examining the tubes, pipes, and wires market in India, we are observing some significant and positive trends. This sector plays a pivotal role in driving infrastructure development, and we expect substantial growth due to the anticipated surge in infrastructure projects across the country. The increasing focus on infrastructure by the Indian government is a strong indicator that these industries will experience a positive impact.
At the moment we are analyzing the market and we see a very good potential because India’s economy is getting stronger and stronger. The government’s strategic decisions to invest in infrastructure further underscore the improvement in the overall infrastructure landscape. Of course, all macroeconomic data indicates positive prospects and India’s trajectory appears quite promising. If the Indian business is good, our business is also good because we are the market leader in India. We have been proactive in embracing the ‘Make in India’ initiative, demonstrating our commitment to the country. Over time, we have developed competencies not only to serve the local Indian market but also to cater to global customers, offering critical process equipment. Our position as a German company hasn’t hindered our belief and investment in local production, staying ahead in supporting India’s industrial aspirations.
TPI: How do you see SMS India’s evolving role in the future?
BS: SMS India, which has deep roots stretching back more than three decades, has grown to embody a unique identity that amalgamates its German heritage with a local presence in the Indian market. As an Indian company, we proudly preserve the DNA inherited from the group while infusing it with a distinctly local touch. This approach is our driving force, allowing us to consistently cater to the specific needs of our customers within the same time zone.
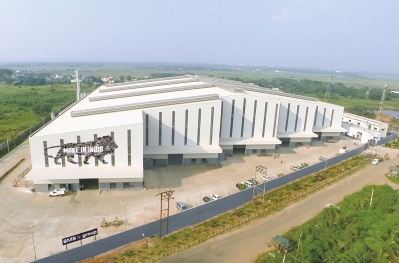
Our commitment to the Indian entity is reflected in our continuous investments in resource development and advanced manufacturing facilities, aimed at enhancing India’s performance to meet global demands. These strategic initiatives over the years have cultivated competencies that provide numerous advantages, leveraging access to local talent, a deep understanding of the culture, and adept knowledge of regional business practices.
Furthermore, our local presence brings a wealth of diversity that optimizes our operations. It allows for swift responses, improved total cost of ownership, and localized services, ultimately enhancing operational efficiency by enabling skilled professionals to work closely with customers and stakeholders.
A pivotal aspect of our customer-centric approach is the provision of round-the-clock (24×7) expert helpline services with remote connectivity. Some recent initiatives have been particularly intriguing:
- Establishment of multiple simulation labs within India for comprehensive testing of hardware and software systems. This ensures faster deployment at sites and facilitates the upskilling of customer teams.
- Introduction of digital solutions that streamline process technologies, providing customers with an entirely new dimension in their operations.
- Expansion of our product portfolio into the non-ferrous space, which plays a crucial role in fostering a circular economy.
- These innovative steps represent SMS India’s continuous evolution, combining global expertise with local dedication, ensuring an ongoing commitment to meeting the diverse and dynamic needs of our customers while remaining at the forefront of technological advancement.