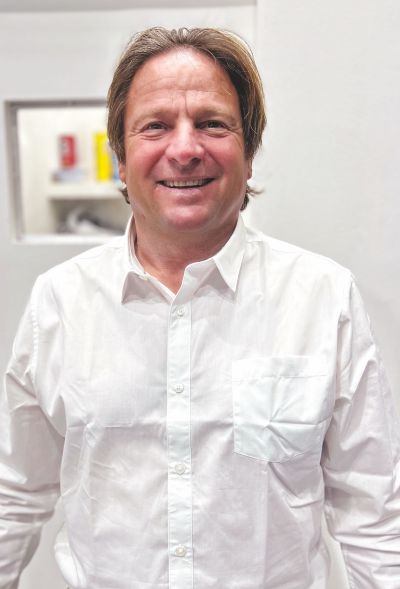
Leading German engineering and manufacturing company- Müller Opladen, rides high on technology, looks at opportunities to make the Indian pipe & tube industry green & plans to enhance its capacity following merger with high-end Voortman Steel Machinery. This was revealed by Mr. Jan Sulimma, Sales Director, Voortman Müller Opladen in his interaction with Tube & Pipe India during Steelfab 2024.
Tube & Pipe India: Shed some light on the merger of Müller Opladen and Voortman Steel Machinery.
Jan Sulimma: Müller Opladen Gmbh is a German engineering and manufacturing company that sold its first pipe profile-cutting machine in 1953. Since then the company has been manufacturing the world’s best CNC profile-cutting machines, for the 3D cutting of steel pipes, vessels and structural steel workpieces, and welding machinery. In 2023, the company considered sustainability and clean energy as the key to keeping itself as relevant and important as it has remained for the last 70 years.
On January 1, 2023, Müller Opladen GmbH became a part of Voortman Steel Machinery, an internationally renowned manufacturer of CNC steel processing machines and innovative software solutions for over 50 years. This acquisition has brought about an expansion of Voortman’s product lineup, as we at Müller bring with us expertise in manufacturing cutting machines for pipes, pressure vessels, and structural steel.
We are thrilled to be joining forces with Voortman as we believe this integration will enable us to improve our offerings significantly. The acquisition strengthens Voortman’s position in the growing offshore & energy, and process equipment markets and allows it to expand its portfolio to include pipe processing technology.
With the merger, we are confident that our valuable knowledge and experience will be instrumental in driving the growth of Voortman as it moves forward. In Mr. Mark Voortman’s, CEO, Voortman Steel Machinery words, “The integration of Müller Opladen is an essential move in meeting the needs of both new and existing customers and offering a complete portfolio for profile, plate, and pipe processing. We are excited to welcome Müller Opladen to the Voortman family and are looking forward to jointly creating new business opportunities and driving future growth.”
TPI: How is the merger going to help Müller Opladen?
JS: We think of it as a very positive development because structurally, Müller was, well, maybe a little bit too small. We sold our machines in 80 countries in the world and this makes service a challenge. So now being part of Voortman worldwide acting group, we have a far bigger network of service points with the Voortman factory and the Voortman Exhibition Center, where we have a big and a small machine. So we have two demo machines nowadays to show to people actually there in a very nice environment.
We are based in Germany, while Voortman is in Holland. It’s only two hours from our actual factory. As a small company, we had the challenge of integrating all these newer, more complex software solutions with our machines. These are things which were very difficult for us to achieve being a small standalone company. So, the backup is very good. We are sure our sales and service will improve as we become part of a bigger company with a bigger footprint in the world.
TPI: Please give information about your manufacturing setup and production capacity.
JS: We have already increased our manufacturing capacity. We are also integrating our production process into the Voortman system. Voortman has a lot of in-house fabrication, while Müller has always outsourced everything. Now we are incorporating this little by little into our machines as well, and the whole process has become more efficient.
TPI: Kindly share information about your market footprint and clientele.
JS: We have customers in over 80 countries worldwide. Our clientele includes companies from the oil and gas sector, all types of piping companies that require pipe cutting systems, refinery-building companies, ship-building companies, etc. Müller Opladen has been in the top segment for pipe cutting machines, which already has a very good place in the Indian market. We sold a machine to the very ambitious VKBS Group recently. The company is set to establish four to five factories for the production of clean energy equipment in India. They have a very modern installation, basically zero CO2 footprint plant with solar panels and integrated into building air conditioning systems. We are aware that our biggest competition in the Indian market is Chinese manufacturers, which exports mechanical solutions at far more economical cost. However, we are glad that VK Group saw the sustainability and benefit in purchasing better and long-term technology. We are going very well on the pipe cutting side.
TPI: Do you have any upcoming product launches or expansions in the pipeline industry?
JS: There are some normal developments on our machines. We are improving our products continuously.
Also Read: SOMO Produzione: Providing Perfect Solutions for Steel Pipe Manufacturers
TPI: What, according to you, are the major challenges and opportunities if we talk about the Indian tube and pipe industry?
JS: We guess the challenge is still the point of moving away from manual pipe cutting into CNC and automated pipe cutting. Obviously, this requires some capital investment, but as the outcome at our customer VKBS shows, it brings far better quality and reliability in your product, along with a lot of positive things about automation. We believe this is more and more reckoned in the Indian market as well.
TPI: Please share your thoughts about the green steel policy of the Government.
JS: It is definitely a very positive development. We are sure our pipe cutting machines can play a good role in all these CO2 free heating and cooling systems. There’s a lot of piping involved and if you can do the piping more efficiently with good machinery, then maybe it’s easier to turn into a green industry.