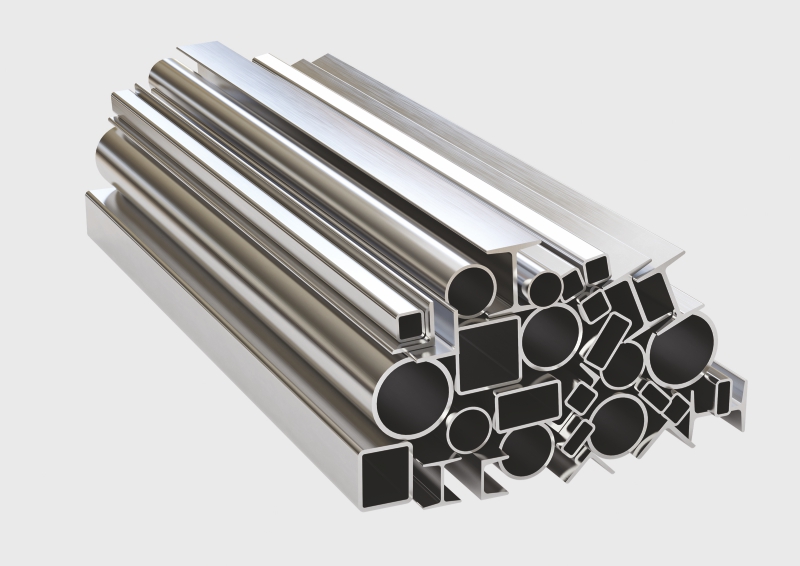
Arora Technologies Private Limited focuses on manufacturing and distribution of Non-Destructive Testing (NDT) products and accessories for global markets. Collaborating with FLUKE Reliability/Prüftechnik NDT GmbH, Arora Technologies has over 90 successful installations in eddy current testing and magnetic flux leakage testing systems throughout India, and has firmly established itself as a frontrunner in developing cutting-edge and practical solutions for testing various types of semi-finished metal tubes, bars, and wires. In a conversation with Tube & Pipe India magazine, Mr. Ronny Lasner, Global Channel Sales Manager, FLUKE Reliability / Prüftechnik NDT GmbH; Mr. Mukesh Arora, Director & CEO, Arora Technologies Private Limited; Mr. Chetan Kale, Team Leader, Manufacturing & Automation Sales, Arora Technologies Private Limited; Ms. Shreya Karade, Business Development Engineer, Arora Technologies Private Limited; emphasized on the current scenario of the steel industry, importance of Non-Destructive Testing (NDT), how to choose correct testing equipment and their product portfolio.
Current Scenario of Steel Industry
Steel is being used as a raw material and an intermediary product in various sectors. Production and consumption of steel have been seen as measures of contribution to technological development. The per capita consumption of steel in India is around 77.2kg, which is 1/3rd of the average world per capita consumption of 233kg. India is the second largest crude steel producer in the world, with a production of 118.1 million tons. However, the per capita consumption of 77.2kg in India, has gone up by 50% in the last 8 years and the rest of the major produced steel is being exported which is around 50-60%. Flat steel products like steel and plates and long steel products like bars, wire rods, structural and rails, each account for 46% of total global shipments, while pipes and tubes have a share of 8%. More than 50% is involved in the manufacturing of steel, bars, wires, tubes, pipes, sheets, etc within India which proves to be a dominant position with respect to other economic sources of the nation.
Why Non-Destructive Testing (NDT) is Important
Before considering any material into practice, it is important to check the quality of the material. Non-destructive testing is a critical tool in ensuring safety and quality. It can be used to test for a variety of potential problems, from cracks and other defects to manufacturing issues. By catching these problems early, NDT can help avoid costly repairs or replacements down the line.
Also Read: Inoxium Tubi: Acing Stainless Steel Tubes & Pipes Manufacturing in the Gulf
What is Eddy Current Testing (ECT)
ECT is one of several Non-Destructive-Testing (NDT) methods that generally allow thorough but harmless inspection of materials without actually touching them or requiring its destruction during sampling. ECT uses minor electro-magnetic induction and can inspect conductive metal or steel materials – either semi-finished or finished goods, for structural defects, damages, cracks, inclusions on the surface or subsurface. Today it is an internationally well accepted testing method in the steel and metal processing industry. Pruftechnik ECT products specialize in the testing or inspection of semi-finished metal or steel materials during their longitudinal production or shaping, such as steel tube, bar, wire, or hot wire, both for inline or offline production processes.
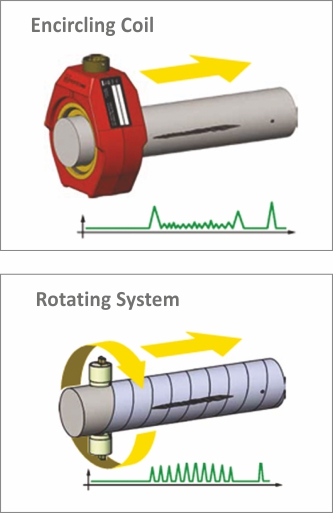
How to Choose the Correct Equipment
There are various parameters that should be considered while selecting specific equipment to carry out a smooth inspection. Majorly for tubes, bars and wires the defects seen are circumferential and longitudinal defects. For a circumferential defect in a metallic material, NDT inspection can be done conveniently using an encircling coil eddy system. In encircling coil eddy current inspection, the product is passed through or adjacent to an electrical test coil, which has been excited by an alternating current. This induces a flow of eddy currents around the test material or in the case of a sector coil, in the area under the coil. Short, intermittent anomalies or flaws cause a variation in the eddy current pattern, which the instrument detects. For longitudinal defects, rotating head eddy current testing is carried out. The rotating system scans the surface of the product to be inspected without contact. Due to the high resolution and the orientation of the probes perpendicular to the cracks, these systems are capable of detecting long, uniform defects unlike encircling coil systems. In the case of both longitudinal and circumferential flaw detection, a complete testing system with the combination of an encircling coil and rotating head system both are used.
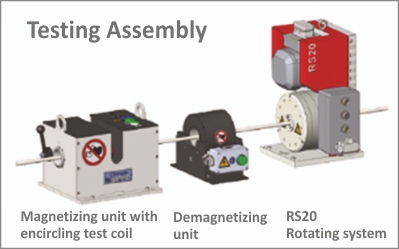
The ultimate solution can be semi-finished products, which are often used in safety-critical parts for public transport, automobiles, construction, etc. where surface condition is a concern, magnetic flux leakage testing.
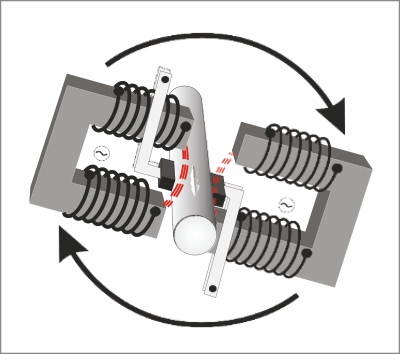
In the Flux leakage method, AC current flows through two rotating magnetizing yokes. The yokes magnetize the test piece at a distance of a few millimeters. Special test shoes with protected probes located between the yoke arms scan the surface of the test piece by sliding over it. The AC magnetic field generates a magnetic flux inside the test piece. If the test piece has an inconsistency in its surface, the magnetic field is deviated and a leakage flux is generated. The sliding probes detect the leakage flux and the NOVAFLUX testing system displays and reports this deviation including exact localization information. In this way, defects as small as 0.1mm can be detected.
Products We Offer
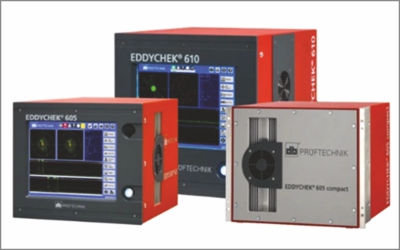
The EDDYCHEK 6 Series includes 3 eddy current testing systems, namely EDDYCHEK 605 COMPACT, EDDYCHEK 605 and EDDYCHEK 610. EDDYCHEK 605 COMPACT is the economic eddy current testing system for reliable quality and process control for the inspection of tubes, bars and wires upto 5 channels and 3 test positions. EDDYCHEK 605 is a reliable, economical, powerful eddy current testing system for advanced quality and process control used in production with a fully digital signal processing up to 5 channels and 3 test positions. EDDYCHEK 610 is a reliable, economical, powerful eddy current testing system for advanced quality and process control used in production with a fully digital signal processing up to 10 channels and 6 test positions.
The NOVAFLUX Inspection System is easy to integrate, reliable, cost saving, compatible, allows testing at high speeds, provides savings on material, and is a cost-effective investment. Based on the flux leakage method, the Novaflux rotating unit finds miniscule surface defects typical for bars and tubes. The defects can be as small as 0.1mm and are distinctly by pseudo signals from uneven surfaces. Integration in the existing production line with inspection speed up to 3m/s and comes with 3 alarm levels with the ease of segregating as per the requirement.
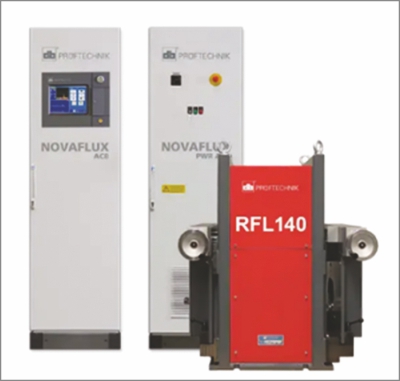
Arora Technologies collaborates with FLUKE Reliability/Prüftechnik NDT GmbH, for developing cutting-edge and practical solutions for testing various types of semi-finished metal tubes, bars, and wires.
rüftechnik NDT GmbH’s expertise spans across their entire production process, enabling them to deliver accurate and reliable testing capabilities for both in-process and final inspections, with over 90 successful installations in eddy current testing and magnetic flux leakage testing systems throughout India. The partnership signifies a shared commitment to provide unmatched solutions that address customer’s specific testing requirements.