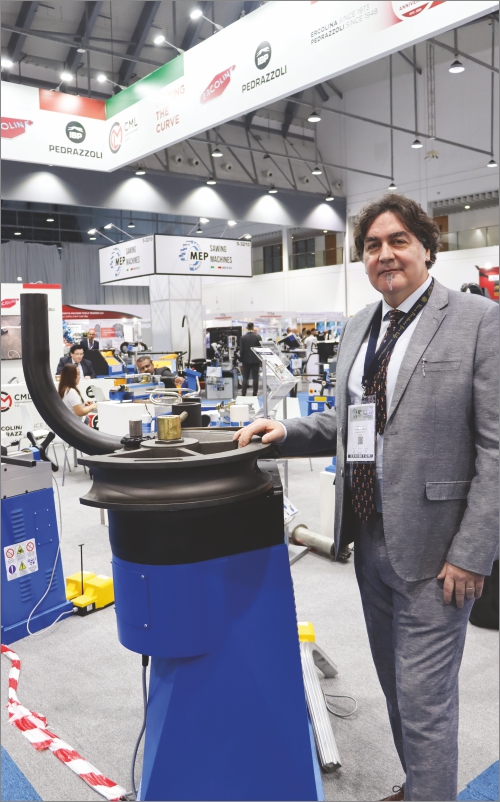
Founded in 1973, CML International S.p.A. started out as an Italian manufacturer of small push-type benders and their line of business includes developing and patenting portable tube bending machines. During an interaction with Tube & Pipe India, Mr. Michael Simonelli – Area Manager, CML International S.p.A., shares the company’s journey, their smart factory infrastructure, innovative no-mandrel machines, industry trends and the company’s future plans in India.
Tube & Pipe India: Could you please give a brief outline of the business journey of your company, along with its crucial milestones?
Michael Simonelli: Our Company was established almost 50 years ago. It started with a simple machine that was used for bending small copper tubes for kitchens and baths. Our products have now evolved into a market that currently serve automotive, ship building, petrochemicals, oil & gas industries. From the small handheld machine for half inch copper tubes in 1974, we’re now bending 8-inch pipes with our fully automatic CNC solutions. So the company has grown considerably in the last few years. In 2018 we purchased a company called Pedrazzoli, who have been in business for 75 years. They were the company that invented the first circular saws in the 1950’s, which has a unique feature that clamps and cuts with a singular motion. From that unique saw, they came up with the first Left/Right-handed bender in 1963. CML-Group of companies have a combined experience of 125 years, offering metal forming/cutting products, from simple manual solutions for metal working shops, to automatic HD shipbuilding and high-end production cells, we are the leaders in the industry for the cold deformation of metals.
TPI: Kindly cast some light on the infrastructure and machinery installed at your facility.
MS: Our facility is a true Smart Factory 4.0 company having approximately 20,000 sq. meters of building, with over 90 machine tools, that are connected via CAD-CAM to our production department. Our technical office is also online with production, which sends/monitors the drawings directly to our machines. That’s where we passionately produce everything, with pride, in our Italian factory near Rome. Regarding our commercial network, we have over 200 partners in almost 80 countries across the globe. We also have branch offices in the United States, South Korea, France, Germany, Singapore and even Russia. However, they’re only distributors, all the machines are made in our office in south-central Italy. Even for our Pedrazzoli products, we manufacture the parts for the machine down in Southern Italy, and then send the finished parts up North to our factory in Bassano Del Grappa, where the machines are completed and tested. From there, the machines are dispatched to their respective destinations.
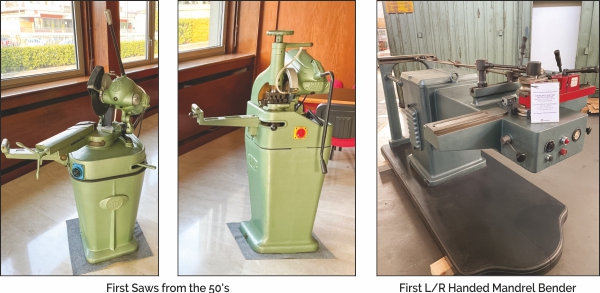
TPI: Could you tell us about the manufacturing capabilities of the company?
MS: For small machines, we sell about 100 machines a month. They are fast moving machines and sell at about 8000-10,000 Euros. As far as the large CNC machines go, the smallest CNC machine we make (the 65-76 size) is manufactured at 2 to 3 machines a month. Larger machines, like the 6-inch gas and up, that is 1 or 2 machines a month. These “mandrel bending machines” have been around since the 1950’s, and we’ve made numerous contributions to this technology such as our patented overhead clamping system and monobloc tunnel design, but what we’re known for is our “non-mandrel machines”. That is where we truly shine. The unique aspect of our no-mandrel machines is its simplicity. We don’t need a mandrel or complicated mechanical systems that require qualified machine operators. With our easy to operate no mandrel benders, simply position a tube to the machine, step on the pedal, and make great looking bends. Not only great looking but performing. Ercolina leads the industry with tight radius bends that have very low ovality, and reduced wall thinning, even with thin wall tubes. And that’s where we’re most popular.
TPI: Tell us about your product portfolio along with its key strengths.
MS: We started off with a small handheld push bender which grew into our first no-mandrel machine. These machines do not require a mandrel, all thanks to the special geometry of our tooling that we are able to make small radius bends even with thin wall tubes. They look great and perform great, we make sure to maintain the wall thickness so that we don’t lose pressure capacity. When you bend with a mandrel, you are stretching the material, thinning the wall and creating a rupture point in the system. Whereas, with our no-mandrel solution we maintain the wall thickness and a good ovality, which is important for the flow of the material. This is because if we have a flat bend, besides the fact that aesthetically it does not look nice, it also performs poorly because that flatness is a restriction in the flow. So with these solutions, we are ASME B36 compliant, with wall thinning and flow regulations. The cost of the machine (with tooling) is equal to just the cost of tooling for a CNC machine. Again, very competitive products as it’s very economical, simple to use and performs very well.
Also Read: Prime Gold: Pioneers of Stainless- Steel Pipes in India
TPI: What are the company’s plans for the Indian market?
MS: Our future plan is to be more active and pertinent with the tube and pipe industry of India. I was recently asked by CML owner why we are not doing more business with BEM (Big Emerging Market) country like India. After some research, I learnt about the Quad coalition, which states that Japan, United States and Australia intend to shift some production to India, diversifying the supply chain instead of depending much on China after the supply chain crisis. I went to Bangalore and Chennai with my Indian partner Sajith of ADM Solutions Pvt and talked to some of our customers who are tier-one automotive suppliers that confirm the automotive industry is gearing up in India and OEM’s are suggesting their suppliers to organize accordingly. From that visit, I am about to close on two large CNC machines of our company’s existing customers who have our smaller machines and are upgrading their productive capacity. So, immediate plans pertinent to India are to increase the market’s knowledge of our solutions, then our involvement with hopefully our sixth branch office. Because I believe the best way to get into large companies of the market is through a direct chain to the main office.
TPI: Please shed some light on the market footprint and the clientele of your company.
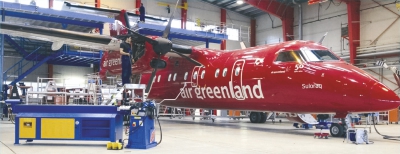
MS: Our machines are well dispersed around the world. We have 200 dealers in 80 countries around the world. In the Middle East, we’ve been exhibiting at the SteelFab expo in Sharjah for years, this is the 7th edition we have participated in, the first with our new partner PassTech who serves the entire G.C.C. From Nuuk Greenland in the Artic, to Nouméa Nuova Caledonia in the South Pacific, I’ve literally sold our fabrication solutions all over the world. In particular, I remember the Air Greenland project to making parts for their helicopters and airplanes with one of our mandrel machines. Though the capital of Greenland, Nuuk is a very isolated area surrounded with ice having only 14 kilometers of road, but not the most desolate home of an Ercolina, we even have one running in Antarctica!
TPI: Please share your insights on the ongoing and future trends in the tubes and pipes industry.
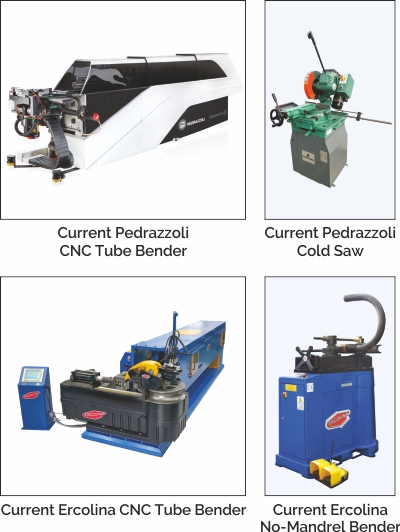
MS: With new technologies, snap-together systems have been created. For example, now when you go to an airport and see handrails, they are assembled parts, not fabricated. There are bends at pre-bent angles that can snap together with a piece of tube to make a handrail. Due to this we are losing a bit of the stainless handrail market. However, we provide solutions to industrial manufacturers and work especially well with petrochemical, shipyards, oil & gas, etc. These sectors don’t only look for aesthetics, but also for performance. When you cold bend, you not only eliminate welding, you also avoid heat treatment to normalize the welding zone; that becomes more brittle during the welding process, x-rays to check and control if there are any holes in the wall, as well as other things like pressure test. Once the QC of the part has been made, then the process of grinding, cleaning, and polishing of the part are to be done afterwards. It is expensive to cut and weld. As you see, when you bend you not only make the component stronger and quicker, it also saves on the considerable costs involved with welding. People do not necessarily consider all aspects involved in part fabrication, that is why our products are very demo oriented. People understand and appreciate the value in it when they see it, therefore I hope you come visit us at the Tube & Pipe Fair in New Delhi this October. I’ll be looking forward to discussing your fabrication requirements with you!